Fusible pattern moulding method of silicon carbide with complicated shape
A technology of shape silicon carbide and molding method, applied in the field of investment molding of complex shape silicon carbide, can solve the problems of low residual carbon rate, unfavorable industrial production, and high price of photosensitive resin
- Summary
- Abstract
- Description
- Claims
- Application Information
AI Technical Summary
Problems solved by technology
Method used
Examples
Embodiment 1
[0011] Embodiment 1: Curing molding: make a paraffin negative mold according to the shape of the silicon carbide part, then mix ethylene glycol and starch evenly in a 1:2 weight ratio to make a pore forming agent; then mix 2130# in a 1:1 weight ratio Thermosetting phenolic resin and pore forming agent are mixed and stirred evenly, then phenolic resin and benzenesulfonyl chloride with a total weight of 8% of ethylene glycol are added and mixed evenly to form a phenolic resin mixture, and the phenolic resin mixture is poured into a paraffin negative mold and left at room temperature The mixture is solidified and shaped to obtain a sample; deep solidification: the solidified sample is heated from an initial temperature of 60°C to 150°C, and the heating rate is 20°C / 12h, and the molten paraffin is recovered at the same time; carbonization: in N 2 Carry out carbonization under gas protection, heat from room temperature to 900°C for 1 hour, and the heating rate is 50°C / h, after compl...
Embodiment 2
[0012] Example 2: Curing molding: Make a paraffin negative mold according to the shape of the silicon carbide part, then mix ethylene glycol and starch evenly at a weight ratio of 1:0.5 to make a pore forming agent; then mix 2130# with a weight ratio of 1:3 Thermosetting phenolic resin and pore forming agent are mixed and stirred evenly, then phenolic resin and benzenesulfonyl chloride with 5% of the total weight of ethylene glycol are added and mixed evenly to make a phenolic resin mixture, and the phenolic resin mixture is poured into a paraffin negative mold, and left at room temperature The mixture is solidified and molded to obtain a sample; deep solidification: the solidified sample is heated from an initial temperature of 60°C to 120°C, and the heating rate is 20°C / 12h, and the molten paraffin is recovered at the same time; carbonization: in N 2 Carry out carbonization under gas protection, heat from room temperature to 700°C for 1 hour, and the heating rate is 50°C / h, a...
Embodiment 3
[0013] Embodiment 3: Curing molding: Make a paraffin negative mold according to the shape of the silicon carbide part, then mix ethylene glycol and starch evenly in a 1:1 weight ratio to make a pore forming agent; then mix 2130# in a 1:1.3 weight ratio Thermosetting phenolic resin and pore forming agent are mixed and stirred evenly, then phenolic resin and 10% benzenesulfonyl chloride by total weight of ethylene glycol are added and mixed evenly to make a phenolic resin mixture, and the phenolic resin mixture is poured into a paraffin negative mold and left at room temperature The mixture is solidified and molded to obtain a sample; deep solidification: the solidified sample is heated from an initial temperature of 60°C to 180°C, and the heating rate is 20°C / 12h, and the molten paraffin is recovered at the same time; carbonization: in N 2 Carry out carbonization under gas protection, heat from room temperature to 1000°C for 1 hour, and the heating rate is 50°C / h, after completi...
PUM
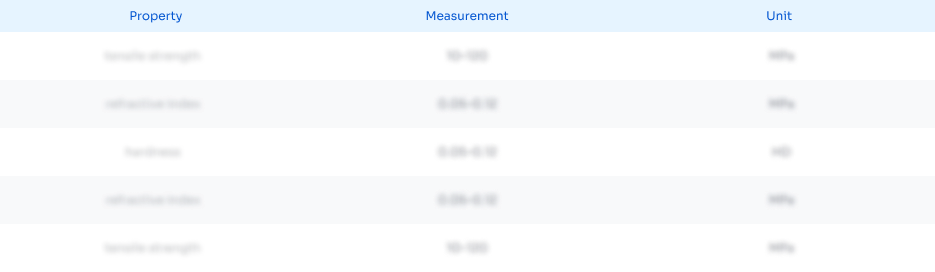
Abstract
Description
Claims
Application Information

- R&D Engineer
- R&D Manager
- IP Professional
- Industry Leading Data Capabilities
- Powerful AI technology
- Patent DNA Extraction
Browse by: Latest US Patents, China's latest patents, Technical Efficacy Thesaurus, Application Domain, Technology Topic, Popular Technical Reports.
© 2024 PatSnap. All rights reserved.Legal|Privacy policy|Modern Slavery Act Transparency Statement|Sitemap|About US| Contact US: help@patsnap.com