Low grade tailing steel slag re-use method and slurry magnetic separation equipment
A low-grade, steel slag technology, applied in clay processing equipment, chemical instruments and methods, magnetic separation, etc., can solve problems such as waste of resources, environment, pollution, etc., and achieve outstanding economic and social benefits.
- Summary
- Abstract
- Description
- Claims
- Application Information
AI Technical Summary
Problems solved by technology
Method used
Image
Examples
Embodiment 1
[0031] Sieve low-grade (total iron content 18%) steel slag with small particle size (less than 10mm), and at the same time, carry out dry magnetic separation of steel slag particles with a size of 5-10mm, and iron slag particles with a size of 5-10mm The recovery rate is 18%, and the recovered scrap iron (40% total iron content) is metallurgically reused, and the steel slag particles with a total iron content below 10% are used as coarse aggregate for the production of standard bricks and porous bricks.
[0032] The steel slag below 5mm and water are mixed in a weight ratio of 1:0.6, plus 2 / 1000 of the total weight of water-reducing grinding aid, and added to a wet ball mill for ball milling. Ball mill until the slurry fineness reaches 0.08mm square hole sieve and the sieve residue is less than 15%, then the iron can be milled and separated, and the steel slag slurry is discharged into the double-chamber magnetic separator for iron separation. The recovery rate of iron powder a...
Embodiment 2
[0038] Sieve low-grade (total iron content 20%) steel slag with small particle size (below 10mm), and at the same time, carry out dry magnetic separation of 5-10mm steel slag particles for iron separation, and 5-10mm steel slag particles for scrap iron The recovery rate is 19.5%. The recovered scrap iron (42% total iron content) is reused in metallurgy, and the steel slag particles with a total iron content below 10% are used as coarse aggregate for standard bricks and porous bricks.
[0039] The steel slag below 5mm and water are mixed according to the weight ratio of 1:0.6, plus 2 / 1000 of the total weight of the water-reducing grinding aid and added to the wet ball mill for ball milling until the fineness of the slurry reaches 0.08mm. If it is less than 15%, it can be used for grinding and selecting iron, and the steel slag slurry is discharged into the double-chamber magnetic separator for iron selection. After cleaning, the recovery rate of iron powder is 13%, and the total...
Embodiment 3
[0045] Sieve low-grade (total iron content 16%) steel slag with small particle size (less than 10mm), and at the same time, carry out dry magnetic separation of 5-10mm steel slag particles for iron separation, and 5-10mm steel slag particles for scrap iron The recovery rate is 17%, and the recovered scrap iron (38% total iron content) is reused for metallurgy, and the steel slag particles with a total iron content below 10% are used as coarse aggregate for producing standard bricks and porous bricks.
[0046] The steel slag below 5mm and water are mixed according to the weight ratio of 1:0.6, plus 2 / 1000 of the total weight of the water-reducing grinding aid and added to the wet ball mill for ball milling until the fineness of the slurry reaches 0.08mm. If the percentage is less than 15%, it can be used for grinding and selecting iron, and the steel slag slurry is discharged into the double-chamber magnetic separator for iron selection. The recovery rate of iron powder after cl...
PUM
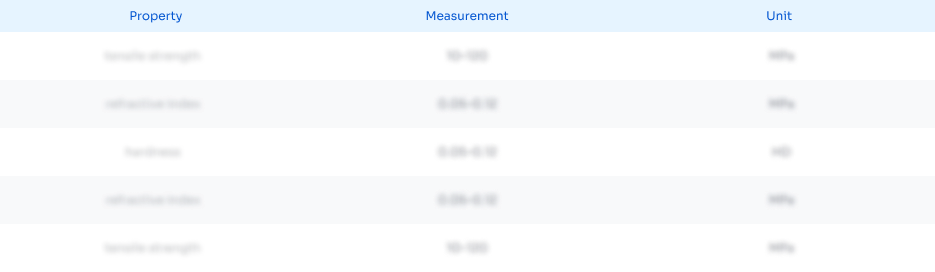
Abstract
Description
Claims
Application Information

- Generate Ideas
- Intellectual Property
- Life Sciences
- Materials
- Tech Scout
- Unparalleled Data Quality
- Higher Quality Content
- 60% Fewer Hallucinations
Browse by: Latest US Patents, China's latest patents, Technical Efficacy Thesaurus, Application Domain, Technology Topic, Popular Technical Reports.
© 2025 PatSnap. All rights reserved.Legal|Privacy policy|Modern Slavery Act Transparency Statement|Sitemap|About US| Contact US: help@patsnap.com