Method for preparing gallium nitride crystal by solid-state displacement reaction
A replacement reaction and gallium nitride technology, applied in chemical instruments and methods, self-solid, crystal growth, etc., can solve the problems of difficult large-scale industrial production, harsh growth conditions, and low crystal growth rate, and achieve easy promotion and The effects of large-scale production, high crystal growth rate, and short synthesis time
- Summary
- Abstract
- Description
- Claims
- Application Information
AI Technical Summary
Problems solved by technology
Method used
Image
Examples
Embodiment 1
[0023] Example 1: Take tetragonal lithium gallate and hexagonal boron nitride pellets with a molar ratio of 1:1, put them into a three-dimensional mixer, mix for about 30 minutes, and press the mixture into a cylindrical block with a mold. Put the pressed cylindrical block into the graphite tube of the pyrophyllite assembly block, and assemble the graphite sheet, molybdenum sheet and conductive steel ring at the upper and lower ends of the graphite tube in sequence. After assembly, place the high-pressure synthetic block in a large-cavity press at a temperature of about 850°C and a pressure of about 1.1GPa. After about 1 minute of heat preservation and pressure holding, the synthetic material is taken out after pressure relief and cooling, and the mass concentration is about Soak in 20% hydrochloric acid to wash out LiBO 2 After waiting for impurities, gallium nitride crystals are obtained.
Embodiment 2
[0024] Example 2: Take tetragonal lithium gallate and hexagonal boron nitride pellets with a molar ratio of 1:0.9, put them into a three-dimensional mixer, mix for about 45 minutes, and press the mixture into a cylindrical block with a mold. Put the pressed cylindrical block into the graphite tube of the pyrophyllite assembly block, and assemble the graphite sheet, molybdenum sheet and conductive steel ring at the upper and lower ends of the graphite tube in sequence. After assembly, place the high-pressure synthetic block in a large-cavity press at a temperature of about 1600°C and a pressure of about 5.0GPa. After about 20 minutes of heat preservation and pressure holding, the synthetic material is taken out after pressure relief and cooling, and the mass concentration is about Soak in 50% nitric acid to wash out LiBO 2 After waiting for impurities, gallium nitride crystals are obtained.
Embodiment 3
[0026] Take the hexagonal phase lithium gallate and hexagonal boron nitride pellets with a molar ratio of 1:0.8, put them into a three-dimensional mixer, mix for about 40 minutes, press the mixture into a cylindrical block with a mold, and put the pressed The cylinder blocks are put into the graphite tube of the pyrophyllite assembly block, and the upper and lower ends of the graphite tube are sequentially assembled with graphite sheets, molybdenum sheets and conductive steel rings. After assembly, place the high-pressure synthetic block in a large-cavity press at a temperature of about 1400°C and a pressure of about 5.5GPa. After about 25 minutes of heat preservation and pressure holding, the synthetic material is taken out after pressure relief and cooling, and the mass concentration is Soak in 30% hydrochloric acid to remove LiBO 2 After waiting for impurities, gallium nitride crystals are obtained.
PUM
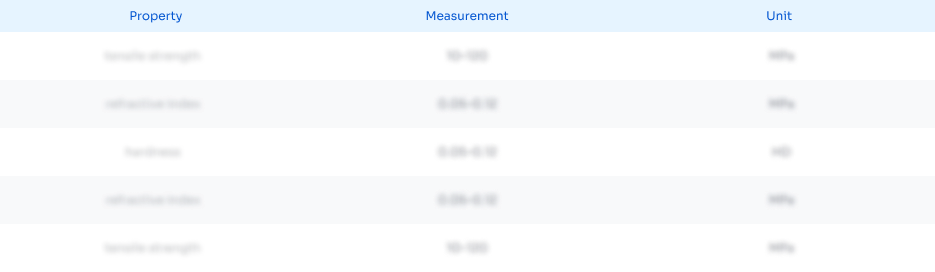
Abstract
Description
Claims
Application Information

- Generate Ideas
- Intellectual Property
- Life Sciences
- Materials
- Tech Scout
- Unparalleled Data Quality
- Higher Quality Content
- 60% Fewer Hallucinations
Browse by: Latest US Patents, China's latest patents, Technical Efficacy Thesaurus, Application Domain, Technology Topic, Popular Technical Reports.
© 2025 PatSnap. All rights reserved.Legal|Privacy policy|Modern Slavery Act Transparency Statement|Sitemap|About US| Contact US: help@patsnap.com