Manganese-zinc ferrite
A manganese-zinc ferrite, weight technology, applied in the field of ferrite, can solve the problems of increased loss, low magnetic permeability, and decreased saturation magnetic flux density, and achieve low loss, high magnetic permeability, low saturation and high Effect of Magnetic Flux Density
- Summary
- Abstract
- Description
- Claims
- Application Information
AI Technical Summary
Problems solved by technology
Method used
Image
Examples
Embodiment 1
[0017] As shown in Table 1, high-purity iron oxide, manganese oxide, and zinc oxide as components were measured and mixed, and pre-fired at 950° C. for 2 hours in the air. Add 0.007% by weight of SiO to the calcined raw material 2 , 0.06% by weight of CaO, 0.04% by weight of Nb 2 o 5 , 0.7% by weight of MgO, 0.3% by weight of CoO, and pulverized with a 1.7 μm sand mill to pulverize the particle size. Thereafter, polyvinyl alcohol was added to the pulverized powder for granulation, and the obtained granulated particles were shaped into rings with an outer diameter of 24 mm, an inner diameter of 19 mm, and a height of 10 mm. Afterwards, control the peak temperature of the oxygen partial pressure in this firing, keep the temperature at 1350° C. for 4 hours and then lower the temperature. After obtaining the sample after firing, measure it with a sand mill to obtain the loss of the sample (100kHz- 200mT and 1MHz—50mT, measuring temperature 23~120℃) and the saturation magnetic f...
Embodiment 2
[0021] The main component of this embodiment adopts the composition combination of example 3 in embodiment 1, and SiO 2 , CaO, Nb 2 o 5 The weight ratio also adopts the ratio in embodiment 1, the ratio of MgO, CoO is adjusted, all the other are consistent with embodiment 1.
[0022] Specifically: according to Fe 2 o 3 : 55.5 mol%, ZnO: 7.0 mol%, and the balance of MnO are measured and mixed with high-purity iron oxide, zinc oxide, and manganese oxide, and pre-fired at 950°C for 2 hours in the atmosphere. And add 0.007% by weight of SiO to this calcined raw material in proportion 2 , 0.06% by weight of CaO, 0.04% by weight of Nb 2 o 5 And add MgO, CoO according to the amount shown in Table 2. Thereafter, samples similar to those in Example 1 were produced and evaluated. In Table 2, the minimum value of loss, temperature and value, saturation magnetic flux density at 23°C and 100°C, and temperature characteristics of loss at 1MHz—50mT are shown. figure 2 It is a schema...
PUM
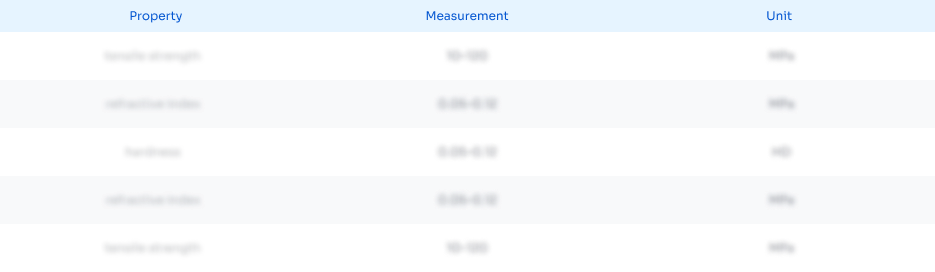
Abstract
Description
Claims
Application Information

- R&D Engineer
- R&D Manager
- IP Professional
- Industry Leading Data Capabilities
- Powerful AI technology
- Patent DNA Extraction
Browse by: Latest US Patents, China's latest patents, Technical Efficacy Thesaurus, Application Domain, Technology Topic, Popular Technical Reports.
© 2024 PatSnap. All rights reserved.Legal|Privacy policy|Modern Slavery Act Transparency Statement|Sitemap|About US| Contact US: help@patsnap.com