Benzin naphtha catalytic reforming method
A technology for catalytic reforming and naphtha, applied in the direction of catalytic reforming of naphtha, control/regulation of reforming operations, etc., can solve the problems of large and insignificant loss of aromatics, increase of BTX yield, etc., and achieve conversion rate High, good selectivity, high yield effect
- Summary
- Abstract
- Description
- Claims
- Application Information
AI Technical Summary
Problems solved by technology
Method used
Image
Examples
preparation example Construction
[0033] The preparation method of the aromatic hydrocarbon lightening catalyst can be prepared by impregnation method, that is, the carrier is impregnated with a solution containing metal components and halogens, then dried, activated with high-temperature water chlorine, and reduced. The method of high-temperature water chlorine activation is to treat the catalyst impregnated with active components with HCl-containing steam, and the H 2 The O / HCl molar ratio is 3-90:1, and the suitable water chlorine activation temperature is 400-800°C, preferably 450-650°C. After the chlorine water is activated, the catalyst is reduced, the gas used for the reduction is hydrogen or carbon monoxide, and the reduction temperature is 250-800°C, preferably 300-500°C.
[0034] The present invention is a kind of improved naphtha catalytic reforming method, if take BTX as target product, because reforming device itself has separated C 6 ~C 8 The fractionation system of the product fraction, the in...
example 1
[0043] This example carries out naphtha catalytic reforming and product separation.
[0044] The continuous reforming catalyst (manufactured by Hunan Jianchang Petrochemical Co., Ltd., brand RC011) is filled in two stages in the reactor of the 200ml test device, with 40ml in the upper stage and 60ml in the lower stage. The naphtha shown in Table 1 is passed into the reforming reactor, and the catalyst has been dried and reduced before feeding. The material flowing out from the reforming reactor passes through the cooler and then enters the high-pressure gas-liquid separator for gas-liquid separation. Part of the separated gas is pressurized by the compressor and then returns to the reforming reactor for circulation. The composition of the reforming catalyst used, the reaction conditions and the composition of the reforming liquid product are shown in Table 2, wherein C 6 ~C 8 Aromatics yield is C 5 + Liquid product yield vs. C 6 、C 7 、C 8 The product of the sum of the a...
example 2
[0053] (1) Preparation of γ-alumina carrier.
[0054] Take 100 grams of aluminum hydroxide powder (brand SB produced by Condea Company) and add 200 grams of deionized water, and stir to make it slurry. Add 7.5 milliliters of nitric acid with a volume ratio of 1:1 per 100 grams of SB powder, add 30 grams of urea and 10 grams of hydrochloric acid solution with a concentration of 36.5 mass%, stir for 1 hour, add 30 grams of kerosene and stir for 1 hour, Dropping balls are formed in the ammonia column. The wet bulb was solidified in ammonia water with a concentration of 6.0% by mass for 1 hour, then filtered, washed 2 to 3 times with deionized water, dried at 60°C for 6 hours, and at 120°C for 10 hours, and then dried in dry air at a ratio of 700:1 The gas / solid volume ratio was calcined at 600° C. for 4 hours to obtain the gamma-alumina carrier.
[0055] (2) Preparation of catalyst
[0056] Take 100 grams of the above-mentioned gamma-alumina carrier, and use the mixed solution...
PUM
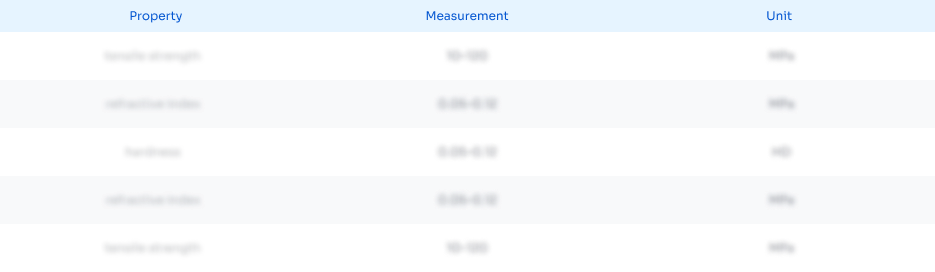
Abstract
Description
Claims
Application Information

- R&D Engineer
- R&D Manager
- IP Professional
- Industry Leading Data Capabilities
- Powerful AI technology
- Patent DNA Extraction
Browse by: Latest US Patents, China's latest patents, Technical Efficacy Thesaurus, Application Domain, Technology Topic, Popular Technical Reports.
© 2024 PatSnap. All rights reserved.Legal|Privacy policy|Modern Slavery Act Transparency Statement|Sitemap|About US| Contact US: help@patsnap.com