Cemented carbide extrusion molding adhesive and preparation thereof
A technology of extrusion molding and cemented carbide, which is applied in the field of cemented carbide extrusion molding binder and preparation, can solve the problems of single binder components, poor degreasing and shape retention performance of forming blanks, etc., and achieve less equipment, Effect of shortening degreasing time and reducing production cost
- Summary
- Abstract
- Description
- Claims
- Application Information
AI Technical Summary
Problems solved by technology
Method used
Examples
Embodiment 1
[0016] The conventional adhesive and the adhesive of the present invention were used for comparison.
[0017] Traditional binder raw material is composed of: 95% paraffin and 5% stearic acid; two groups of binders of the present invention are, group 1: 75% paraffin, 10% styrene-butadiene rubber, 5% dibutyl phthalate Esters, 5% rapeseed oil and 5% stearic acid, the organic solvent is 120 # Gasoline; Group 2: 78% paraffin, 20% styrene-butadiene rubber, 2% dibutyl phthalate, 3% rapeseed oil and 6% stearic acid, the organic solvent is n-hexane.
[0018] The preparation method of present embodiment binding agent is:
[0019] a. At room temperature, use 120 in the sol machine # Dissolve styrene-butadiene rubber in gasoline or n-hexane to make rubber gasoline solution for later use;
[0020] b. Add paraffin wax into the mixer and heat to 65-75°C to melt, then add dibutyl phthalate, rapeseed oil, stearic acid and rubber gasoline solution, and stir for 2-5 minutes to obtain the prod...
Embodiment 2
[0025] The conventional adhesive and the adhesive of the present invention were used for comparison.
[0026] Traditional binding agent consists of: 95% paraffin and 5% stearic acid; two groups of binding agents of the present invention consist of, group 1: 65% paraffin, 15% styrene-butadiene rubber, 3% dibutyl phthalate Esters, 1% rapeseed oil and 3% stearic acid; Group 2: 60% paraffin, 6% styrene-butadiene rubber, 8% dibutyl phthalate, 6% rapeseed oil and 2% stearic acid. The preparation method is the same as in Example 1.
[0027] The experiment adopts the same batch of superfine cemented carbide compound JF10112, which is divided into three groups, one group adopts traditional binding agent (marked as O), and the other two groups adopt the binding agent of group 1 and group 2 of the present invention ( Denoted as N and M), the cemented carbide powder was added to the mixer and mixed, extruded into a rod with a model size of Φ8×300, and degreased under the same conditions....
PUM
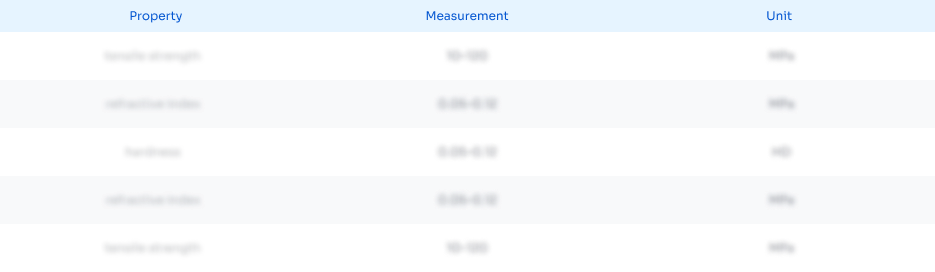
Abstract
Description
Claims
Application Information

- R&D Engineer
- R&D Manager
- IP Professional
- Industry Leading Data Capabilities
- Powerful AI technology
- Patent DNA Extraction
Browse by: Latest US Patents, China's latest patents, Technical Efficacy Thesaurus, Application Domain, Technology Topic, Popular Technical Reports.
© 2024 PatSnap. All rights reserved.Legal|Privacy policy|Modern Slavery Act Transparency Statement|Sitemap|About US| Contact US: help@patsnap.com