Production method of graphite plane commutator
A manufacturing method and commutator technology, which is applied in commutator manufacturing and other directions, can solve problems such as unstable quality, shortened life, and falling off of graphite flakes, and achieve the effect of solving unstable quality, stable work performance, and small deformation of workpieces
- Summary
- Abstract
- Description
- Claims
- Application Information
AI Technical Summary
Problems solved by technology
Method used
Image
Examples
Embodiment Construction
[0025] The end face of the graphite planar commutator mentioned in the present invention refers to the side of the graphite planar commutator facing the brush, that is, the end face of the annular graphite sheet.
[0026] figure 1 Shown is the schematic diagram of the shaped annular graphite sheet 1 of the present invention, figure 2 with image 3 It is a schematic diagram of the structure of the precision copper shell 2 of the present invention. The precision copper shell 2 has a semi-closed cavity, an open end 3 that makes the cavity open outward, and a central axis hole opposite to the open end 3 The working end 5 of 4, a plurality of claws 6 uniformly surrounding the working end 5 with the same size and shape, and the inner claw 7 and the outer claw 8 on the inner surface of the working end 5 facing the open end 3 , each claw 6 corresponds to an inner claw 7 and an outer claw 8, and the inner claw 7 and the outer claw 8 cooperate with each other to form a "eight"-shaped...
PUM
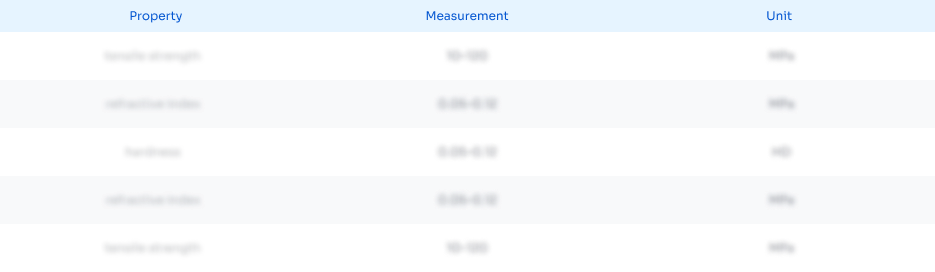
Abstract
Description
Claims
Application Information

- R&D
- Intellectual Property
- Life Sciences
- Materials
- Tech Scout
- Unparalleled Data Quality
- Higher Quality Content
- 60% Fewer Hallucinations
Browse by: Latest US Patents, China's latest patents, Technical Efficacy Thesaurus, Application Domain, Technology Topic, Popular Technical Reports.
© 2025 PatSnap. All rights reserved.Legal|Privacy policy|Modern Slavery Act Transparency Statement|Sitemap|About US| Contact US: help@patsnap.com