Pine gum processing method and equipment
A processing method and technology of processing equipment, applied in the field of pine resin processing, can solve the problems of insufficient utilization of steam, oil and gas heat temperature, fat liquid waste, and low total yield, so as to save energy and dissolution time, improve the quality of fat liquid, and save energy The effect of consumption reduction effect
- Summary
- Abstract
- Description
- Claims
- Application Information
AI Technical Summary
Problems solved by technology
Method used
Image
Examples
Embodiment Construction
[0037] The rosin production process and equipment of the present invention will be further described below in conjunction with the accompanying drawings.
[0038] 1. Rosin production process is as follows:
[0039] exist figure 1 In the process, the turpentine is continuously sent into the turpentine preheating pot through spiral transportation and heated to 60-70°C. The steam supplied by the preheating pot is provided by the closed tail steam of the steam pot, and then sent into the melting pot for heating and melting. The melted turpentine is sent to the high-level pot for transition clarification. The high-position transition pot is injected with increased volume (1:4 ratio) and pressure relief. The turpentine liquid realizes self-fluidization and continuous transition clarification, and then is sent to the clarification pot for further clarification. It is sent to the turpentine liquid preheating pot through the fat liquid filter, and then sent to the distillation operati...
PUM
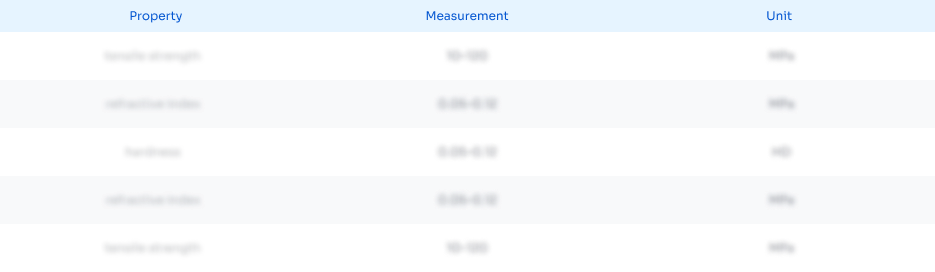
Abstract
Description
Claims
Application Information

- R&D
- Intellectual Property
- Life Sciences
- Materials
- Tech Scout
- Unparalleled Data Quality
- Higher Quality Content
- 60% Fewer Hallucinations
Browse by: Latest US Patents, China's latest patents, Technical Efficacy Thesaurus, Application Domain, Technology Topic, Popular Technical Reports.
© 2025 PatSnap. All rights reserved.Legal|Privacy policy|Modern Slavery Act Transparency Statement|Sitemap|About US| Contact US: help@patsnap.com