Eccentric oscillating-type planetary gear device
A technology of planetary gear and eccentric swing, which is applied in the direction of gear transmission, transmission, friction transmission, etc. It can solve the problems of low rigidity, shortened service life of the tooth surface of the external gear 101, and cannot fully increase the output torque, etc., and achieves the purpose of extending the gear Improve surface life, increase natural vibration frequency, improve vibration characteristics and controllability
- Summary
- Abstract
- Description
- Claims
- Application Information
AI Technical Summary
Problems solved by technology
Method used
Image
Examples
Embodiment 1
[0058] Embodiment 1 of the present invention will be described below with reference to the drawings.
[0059] exist figure 1 , figure 2 Among them, 11 is an eccentric oscillating planetary gear device used in a robot or the like, and the planetary gear device 11 has a substantially cylindrical rotating housing 12 attached to, for example, an arm or hand of a robot not shown in the figure. A plurality of roller (pin) grooves 13 having a semicircular cross-section at the central portion in the axial direction are formed on the inner periphery of the rotating housing 12. These roller grooves 13 extend in the axial direction and are separated at equal distances in the circumferential direction. It is arranged separately with a certain tooth pitch P. 14 is an internal tooth composed of a plurality of cylindrical rollers (the same number as the roller grooves 13), and approximately half of these internal teeth (rollers) 14 are inserted into the roller groove 13, so that Equidis...
Embodiment 2
[0092] Figure 7 , 8 It is a figure which shows Example 2 of this invention. In this second embodiment, the outer teeth 19 are not removed as in the first embodiment, but the inner circumference of the internal gear 15 (rotary casing 12) between adjacent internal teeth (rollers) 14 and the inner circumference of each The inner circumference around the inner teeth (roller) 14 is cut off to a depth greater than the amount by which the outer teeth 19 exceed the inner circumference. This avoids interference between the external teeth 19 and the inner periphery 15a of the internal gear 15 (rotary casing 12) after removal.
[0093] As a result, the radially outer end of each internal tooth (roller) 14 is in line contact with the inner periphery 15a of the internal gear 15 after removal, whereby the rotating housing 12 receives the driving force component acting on each internal tooth (roller) 14 The force component in the radial direction of . At this time, since there is no rol...
Embodiment 3
[0097] Embodiment 3 of the present invention will be described below with reference to the drawings.
[0098] exist Figure 9 , 10 In , 11, 111 is an eccentric oscillating planetary gear device for a robot or the like, and the planetary gear device 111 has a substantially cylindrical rotating housing 112 mounted on an arm, hand, etc. of a robot not shown in the figure. A plurality of roller grooves 113 having a semicircular cross-section at the central portion in the axial direction are formed on the inner periphery of the rotary housing 112 , and the roller grooves 113 extend in the axial direction and are arranged at equal distances in the circumferential direction. 114 is an internal tooth composed of a plurality (the same number as the roller groove 113) of cylindrical rollers, and about half of these internal teeth (rollers) 114 are inserted into the roller groove 113, so they are spaced apart in the circumferential direction, etc. The distance is set on the inner circu...
PUM
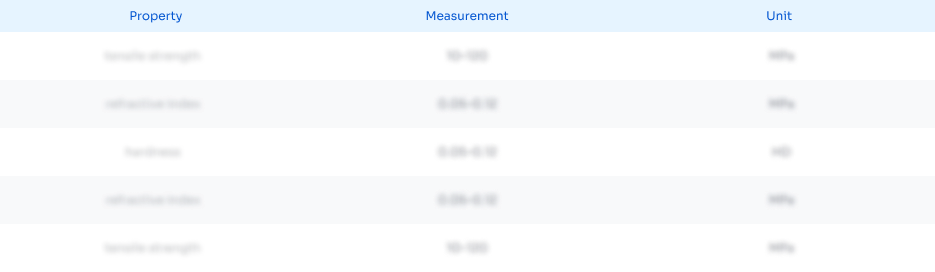
Abstract
Description
Claims
Application Information

- Generate Ideas
- Intellectual Property
- Life Sciences
- Materials
- Tech Scout
- Unparalleled Data Quality
- Higher Quality Content
- 60% Fewer Hallucinations
Browse by: Latest US Patents, China's latest patents, Technical Efficacy Thesaurus, Application Domain, Technology Topic, Popular Technical Reports.
© 2025 PatSnap. All rights reserved.Legal|Privacy policy|Modern Slavery Act Transparency Statement|Sitemap|About US| Contact US: help@patsnap.com