Process for comprehensive recovery nickel, copper, cobalt, sulfur and magnesium from ore
A kind of ore and process technology, applied in the direction of sulfur preparation/purification, process efficiency improvement, etc., can solve the problems of energy consumption, large energy consumption, air pollution, etc., and achieve the effect of reducing energy consumption and avoiding air pollution
- Summary
- Abstract
- Description
- Claims
- Application Information
AI Technical Summary
Problems solved by technology
Method used
Image
Examples
Embodiment Construction
[0035] Embodiments of the present invention are described in detail below, examples of which are illustrated in the accompanying drawings, wherein like reference numerals refer to like elements throughout. The embodiments are described below in order to explain the present invention by referring to the figures, which are exemplary and should not be construed as limitations of the present invention.
[0036] The process of comprehensively recovering nickel, copper, cobalt, sulfur and magnesium from high-magnesium-nickel concentrate according to the embodiment of the present invention will be described below with reference to the accompanying drawings.
[0037] Such as Figure 4 and Figure 5 As shown, at first, the copper-nickel-containing ore is obtained through preliminary crushing, screening, and flotation ore to obtain a high-magnesium-nickel concentrate with low copper-nickel content and high magnesium oxide. This high-magnesium-nickel concentrate mainly contains nickel (...
PUM
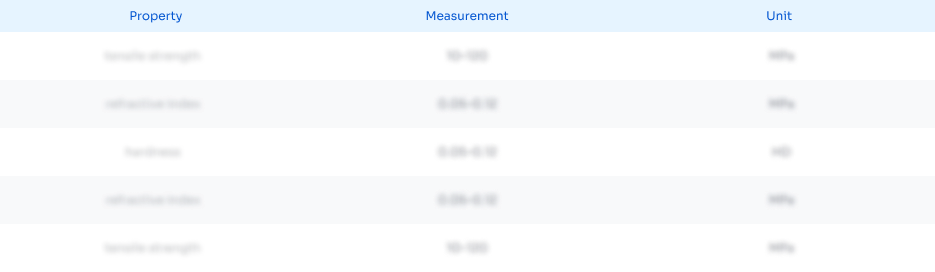
Abstract
Description
Claims
Application Information

- R&D
- Intellectual Property
- Life Sciences
- Materials
- Tech Scout
- Unparalleled Data Quality
- Higher Quality Content
- 60% Fewer Hallucinations
Browse by: Latest US Patents, China's latest patents, Technical Efficacy Thesaurus, Application Domain, Technology Topic, Popular Technical Reports.
© 2025 PatSnap. All rights reserved.Legal|Privacy policy|Modern Slavery Act Transparency Statement|Sitemap|About US| Contact US: help@patsnap.com