Method and apparatus for lubricating grease continuous saponification
A lubricating grease and saponification technology, which is applied in the field of continuous saponification of lubricating grease and its device, can solve the problems of long reaction time, high production cost, poor temperature control, etc., achieve long circuitous lines, prevent product volatilization loss, heat The effect of large exchange area
- Summary
- Abstract
- Description
- Claims
- Application Information
AI Technical Summary
Problems solved by technology
Method used
Image
Examples
Embodiment Construction
[0016] A method for continuous saponification of grease, as shown in Figure 1 and Figure 2, comprises the steps:
[0017] (1) Grease and soap-based chemical raw materials are added in the raw material blending tank 1 with agitator 2, and stirred evenly;
[0018] (2) Pump the logistics in the raw material blending tank 1 into the heat exchange elbow 7 of the curved tube type heat exchange tank 6 heated by the high temperature heat transfer oil provided by the heating oil furnace 4, and exchange heat with the heat transfer oil in the tank, The temperature of the heated stream is 210°-280°C, and the flow velocity of the stream in the heat exchange curved tube 7 is 2.5-3.5 m / s;
[0019] (3) The saponified grease is discharged from the outlet of the curved tube type heat exchange tank 6 and pumped into the soap-based chilling tank 12 with the agitator 2, chilled and stirred evenly, and sheared by the needle shears 13, The flow rate of the lubricating grease entering the soap base ...
PUM
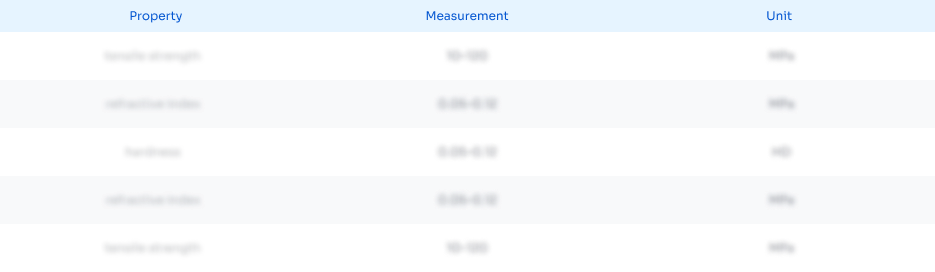
Abstract
Description
Claims
Application Information

- R&D
- Intellectual Property
- Life Sciences
- Materials
- Tech Scout
- Unparalleled Data Quality
- Higher Quality Content
- 60% Fewer Hallucinations
Browse by: Latest US Patents, China's latest patents, Technical Efficacy Thesaurus, Application Domain, Technology Topic, Popular Technical Reports.
© 2025 PatSnap. All rights reserved.Legal|Privacy policy|Modern Slavery Act Transparency Statement|Sitemap|About US| Contact US: help@patsnap.com