Method for preparing methanol using coal bed gas
A technology for coalbed methane and methanol, applied in chemical instruments and methods, preparation of hydroxyl compounds, preparation of organic compounds, etc., to achieve the effects of reducing pollution, low price, and low environmental pollution
- Summary
- Abstract
- Description
- Claims
- Application Information
AI Technical Summary
Problems solved by technology
Method used
Image
Examples
Embodiment 1
[0018] Raw coalbed methane 5000Nm 3 / h, the composition (volume percentage, the same below) is: 40% CH 4 , 12% O 2 , 48%N 2 , pressurize to 0.3MPa, add water vapor 4821.4Kg / h, the molar ratio of added water vapor to methane in coalbed methane is: H 2 O / CH 4 =3, preheated to 500°C, sent to the autothermal reforming reactor equipped with Ni-based catalyst, using CH 4 with O 2 The heat of combustion makes part of the CH 4 Converted to H with water vapor in the presence of Ni-based catalyst 2 and CO; the gas from the thermal conversion reactor enters the external thermal conversion reactor equipped with a Ni-based catalyst, and the external thermal reformer is heated by coalbed methane to further convert the remaining methane in the coalbed methane into H 2 and CO, the outlet temperature of the external thermal reformer is 800°C, and the composition of the reformed gas is: H 2 56%, N 2 24%, CH 4 0.5%, CO 11.2%, CO 2 8.3%, gas volume 10000Nm 3 / h; the heat is recovered ...
Embodiment 2
[0020] Raw coalbed methane 5000Nm 3 / h, composition: 50% CH 4 , 10% 0 2 , 40%N 2 , pressurize to 0.6MPa, add water vapor 8036Kg / h, the molar ratio of added water vapor to methane in coalbed methane is: H 2 O / CH 4 =4, preheated to 500°C, sent to the autothermal reforming reactor equipped with Ni-based catalyst, using CH 4 with O 2The heat of combustion makes part of the CH 4 Converted to H with water vapor in the presence of Ni-based catalyst 2 and CO; the gas from the thermal conversion reactor enters the external thermal conversion reactor equipped with a Ni-based catalyst, and the external thermal reformer is heated by the purge gas of coalbed methane and methanol, so that the remaining methane in the coalbed methane is further converted into H 2 and CO, the temperature at the outlet of the external thermal reformer is 820°C, and the reformed gas composition is: H 2 62.8%, N 2 16.5%, CH 4 0.4% CO 10.4% CO 2 9.9%, gas volume 12122Nm 3 / h;
[0021] The heat is rec...
Embodiment 3
[0023] Raw coalbed methane 5000Nm 3 / h, composition: 50% CH 4 , 10%O 2 , 40%N 2 , pressurize to 0.6MPa, add water vapor 6027Kg / h, the molar ratio of added water vapor to methane gas in coalbed methane is: H 2 O / CH 4 =3, preheated to 600°C, sent to the autothermal reforming reactor equipped with Ni-based catalyst, using CH 4 with O 2 The heat of combustion makes part of the CH 4 Converted to H with water vapor in the presence of Ni-based catalyst 2 and CO; the gas from the thermal conversion reactor enters the external thermal conversion reactor equipped with a Ni-based catalyst, and the external thermal reformer is heated by the purge gas of coalbed methane and methanol, so that the remaining methane in the coalbed methane is further converted into H 2 and CO, the temperature at the outlet of the external thermal reformer is 840°C, and the reformed gas composition is: H 2 61.98%, N 2 16.9%, CH 4 0.43%, CO 12.34%, CO 2 8.35%, gas volume 11835Nm 3 / h;
[0024] Heat ...
PUM
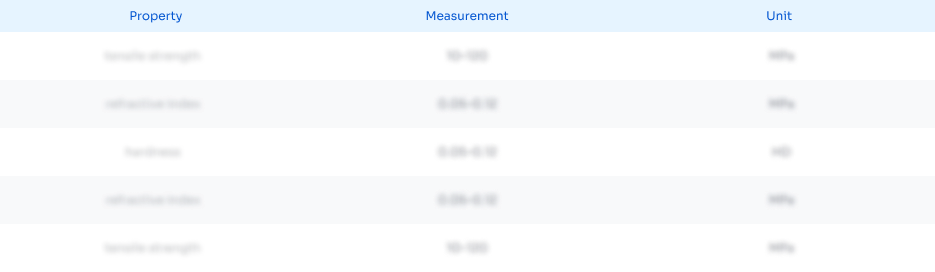
Abstract
Description
Claims
Application Information

- R&D
- Intellectual Property
- Life Sciences
- Materials
- Tech Scout
- Unparalleled Data Quality
- Higher Quality Content
- 60% Fewer Hallucinations
Browse by: Latest US Patents, China's latest patents, Technical Efficacy Thesaurus, Application Domain, Technology Topic, Popular Technical Reports.
© 2025 PatSnap. All rights reserved.Legal|Privacy policy|Modern Slavery Act Transparency Statement|Sitemap|About US| Contact US: help@patsnap.com