Preparation method of catalyst for acrylonitrile fluid bed
An acrylonitrile fluidized bed and catalyst technology, which is used in physical/chemical process catalysts, hydrocarbon ammoxidation preparation, chemical instruments and methods, etc. and other problems to achieve the effect of ensuring long-term effect and high activity selectivity
- Summary
- Abstract
- Description
- Claims
- Application Information
AI Technical Summary
Problems solved by technology
Method used
Image
Examples
Embodiment 1
[0083] Get 415 grams of ammonia-stabilized concentration 40% SiO 2 Silica sol, add 17 grams of tetraethylamine and make material A after fully stirring; 384.4 grams of ammonium molybdate are dissolved in 200 milliliters of water, make material B; 125 grams of iron nitrate, 72.9 grams of bismuth nitrate, 331.9 grams of nickel nitrate, 100 grams Magnesium nitrate, 18.9 grams of copper nitrate are dissolved in 600 milliliters of water to obtain material C; 1.3 grams of lithium nitrate, 10.9 grams of cesium nitrate, and 0.7 gram of arsenic acid are dissolved in 10 milliliters of water to obtain material D; Add D into A, stir well, adjust the pH value to 1.5 with 10% ammonia water, heat to 80°C, and the gauge pressure is 0.4MPa, spray dry and shape after 6 hours, transfer to the cremation furnace, heat up to 320°C, heat Decompose for 2 hours; heat up to 420°C, crystal phase transition for 8 hours; heat up to 580°C, activate and roast for 4 hours, cool to room temperature after acti...
Embodiment 2
[0088] Take 467 grams of ammonia stable concentration 40% SiO 2 Silica sol, add 24 grams of tetrapropylammonia and make material A through fully stirring; 384.4 grams of ammonium molybdate are dissolved in 200 milliliters of water, make material B; 100 grams of iron nitrate, 36.5 grams of bismuth nitrate, 258.1 grams of nickel nitrate, 66.7 Gram magnesium nitrate, 5.6 gram chromium nitrates are dissolved in 600 milliliters of water, make material third; 1.8 gram potassium nitrate, 0.5 gram boric acid, 4.8 gram beryllium nitrates are dissolved in 10 milliliters of water and make material D, will make material second, third, Add D into A, stir well, adjust the pH value to 1.5 with 10% ammonia water, heat to 60°C, and the gauge pressure is 0.2MPa, spray dry and shape after 8 hours, transfer to the cremation furnace, heat up to 290°C, heat Decompose for 2 hours; heat up to 440°C, crystal phase transition for 6 hours; heat up to 600°C, activate and roast for 2 hours, cool to room t...
Embodiment 3
[0093] Get 518 grams of ammonia stable concentration 40% SiO 2 Silica sol, add 10 grams of polyacrylamide, make material A through thorough stirring; 384.4 grams of ammonium molybdates are dissolved in 200 milliliters of water, make material B; 75 grams of ferric nitrate, 109.4 grams of bismuth nitrate, 184.4 grams of nickel nitrate, 33.3 Gram magnesium nitrate, 4.4 gram vanadic acid are dissolved in 600 milliliters of water, make material third; 1.4 gram phosphoric acid, 2.1 gram stannic acid, 4.9 gram cesium nitrate are dissolved in 10 milliliters of water and make material D, will make material second, third, Add D into A, stir well, adjust pH value to 2 with 10% ammonia water, heat to 100°C, gauge pressure 0.6MPa, carry out spray drying and molding after 4 hours, transfer to cremation furnace, heat up to 300°C, heat Decompose for 2 hours; heat up to 440°C, crystal phase transition for 8 hours; heat up to 620°C, activate and roast for 2 hours, cool to room temperature after...
PUM
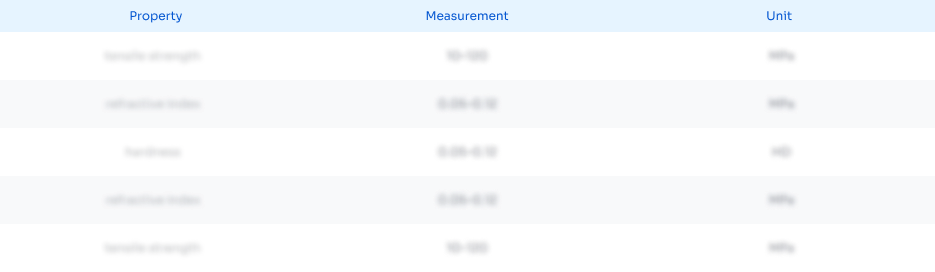
Abstract
Description
Claims
Application Information

- R&D Engineer
- R&D Manager
- IP Professional
- Industry Leading Data Capabilities
- Powerful AI technology
- Patent DNA Extraction
Browse by: Latest US Patents, China's latest patents, Technical Efficacy Thesaurus, Application Domain, Technology Topic, Popular Technical Reports.
© 2024 PatSnap. All rights reserved.Legal|Privacy policy|Modern Slavery Act Transparency Statement|Sitemap|About US| Contact US: help@patsnap.com