Process control technology for vacuum brazing aluminum alloy composite board belt foil
A composite strip and control technology, which is applied in metal rolling and other directions, can solve problems such as cracking and leaking points, and achieve the effects of firm welds, increased fluidity, increased fluidity and diffused flow
- Summary
- Abstract
- Description
- Claims
- Application Information
AI Technical Summary
Problems solved by technology
Method used
Examples
Embodiment Construction
[0018] In order to make the above objects, features and advantages of the present invention more comprehensible, the present invention will be further described in detail below in conjunction with specific embodiments.
[0019] When the aluminum alloy is smelted, various metals or additives are added in sequence according to the chemical composition requirements of the ingot, including the aluminum-bismuth master alloy with a bismuth content of 3%. All the components of the ingot are controlled within the range required by the standard, and the bismuth content is controlled between 0.05-0.15%. The above-mentioned smelting process is the prior art; when rolling the brazed composite layer slabs, they are made into 40, 50, 60mm thickness respectively, compounded on the core material of 265, 265, 240mm, and the cladding rate is 12% after rolling. , 14%, 16% composite strips. The rolling process is the same as the existing process, and will not be repeated here.
[0020] Bismuth ...
PUM
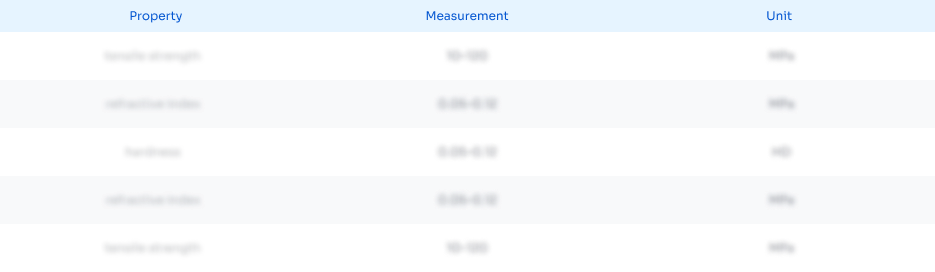
Abstract
Description
Claims
Application Information

- Generate Ideas
- Intellectual Property
- Life Sciences
- Materials
- Tech Scout
- Unparalleled Data Quality
- Higher Quality Content
- 60% Fewer Hallucinations
Browse by: Latest US Patents, China's latest patents, Technical Efficacy Thesaurus, Application Domain, Technology Topic, Popular Technical Reports.
© 2025 PatSnap. All rights reserved.Legal|Privacy policy|Modern Slavery Act Transparency Statement|Sitemap|About US| Contact US: help@patsnap.com