Moisture absorption perspiration-discharging dressing agent and its manufacturing technique and application
A technology of moisture absorption and perspiration and finishing agent, which is applied in fiber treatment, textiles and papermaking, fiber types, etc., and can solve the problems of poor wearability, polyester fiber moisture absorption and perspiration, antistatic performance, easy decontamination performance, and poor fluffy softness, etc. problems, to achieve the effect of improving the modification effect, good moisture absorption and perspiration, and improving comfort
- Summary
- Abstract
- Description
- Claims
- Application Information
AI Technical Summary
Problems solved by technology
Method used
Examples
Embodiment 1
[0026] 1) Take by weighing 800 grams of polyethylene glycol, 150 grams of ethylene glycol, 150 grams of polyether, 180 grams of dimethyl terephthalate, and 10 grams of catalyst;
[0027] 2) Put polyethylene glycol, ethylene glycol and polyether into the reaction kettle, and heat the reaction kettle, and start vacuuming when the temperature rises to 75°C, so that the vacuum degree in the kettle reaches -0.090MPa, and then continue to heat up to 90°C, keep warm for 50 minutes, then raise the temperature to 102°C, put dimethyl terephthalate and catalyst into the reactor, continue to raise the temperature to 150°C, and keep it for 60 minutes, so that the materials in the reactor are fully esterified, Then press the esterified material in the reaction kettle into the polymerization kettle, under the conditions of vacuum degree of -0.095MPa and temperature of 220°C, and under the catalysis of metal acetate salt, after 40 minutes of polymerization, the molecular weight is 30,000-50,0...
Embodiment 2
[0029] 1) Take by weighing 900 grams of polyethylene glycol, 120 grams of ethylene glycol, 120 grams of polyether, 165 grams of dimethyl terephthalate, and 5 grams of catalyst;
[0030] 2) Put polyethylene glycol, ethylene glycol and polyether into the reaction kettle, and heat the reaction kettle, and start vacuuming when the temperature rises to 78°C, so that the vacuum degree in the kettle reaches -0.093MPa, and then continue to heat up to 95°C, keep warm for 55 minutes, then raise the temperature to 104°C, put dimethyl terephthalate and catalyst into the reactor, continue to raise the temperature to 155°C, and keep it for 75 minutes, so that the materials in the reactor are fully esterified, Then press the esterified material in the reaction kettle into the polymerization kettle, under the conditions of vacuum degree of -0.098MPa and temperature of 240°C, and under the catalysis of metal acetate salt, after 50 minutes of polymerization, the molecular weight is 30,000-50,00...
Embodiment 3
[0032] 1) Take by weighing 1000 grams of polyethylene glycol, 100 grams of ethylene glycol, 100 grams of polyether, 150 grams of dimethyl terephthalate, and 3 grams of catalyst;
[0033] 2) Put polyethylene glycol, ethylene glycol and polyether into the reaction kettle, and heat the reaction kettle, and start vacuuming when the temperature rises to 80°C, so that the vacuum degree in the kettle reaches -0.095MPa, and then continue to heat up to 100°C, keep warm for 60 minutes, then raise the temperature to 106°C, put dimethyl terephthalate and catalyst into the reactor, continue to raise the temperature to 160°C, and keep it for 90 minutes, so that the materials in the reactor are fully esterified, Then press the esterified material in the reaction kettle into the polymerization kettle, under the conditions of vacuum degree of -0.1MPa and temperature of 250°C, and under the catalysis of metal acetate salt, after 60 minutes of polymerization, the molecular weight is 30,000-50,00...
PUM
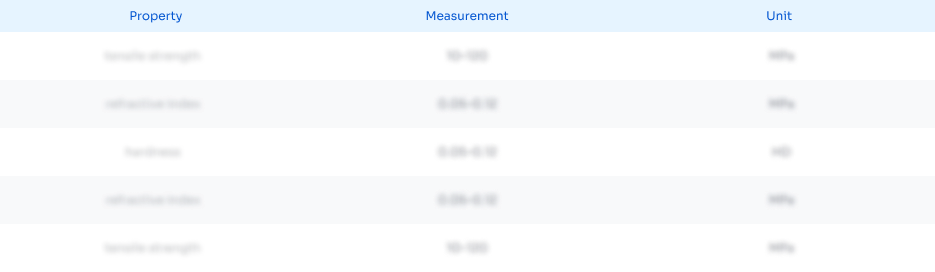
Abstract
Description
Claims
Application Information

- R&D
- Intellectual Property
- Life Sciences
- Materials
- Tech Scout
- Unparalleled Data Quality
- Higher Quality Content
- 60% Fewer Hallucinations
Browse by: Latest US Patents, China's latest patents, Technical Efficacy Thesaurus, Application Domain, Technology Topic, Popular Technical Reports.
© 2025 PatSnap. All rights reserved.Legal|Privacy policy|Modern Slavery Act Transparency Statement|Sitemap|About US| Contact US: help@patsnap.com