Continuous catalysis cracking method for producing fuel oil from mixed waste plastic
A technology of catalytic cracking and waste plastics, which is applied in the field of fuel oil preparation from mixed waste plastics. It can solve the problems of high energy consumption in the heating and cooling process, the inability to form continuous operations, and unstable oil quality. It achieves low operating costs and considerable economy. and social benefits, reducing raw material costs and manufacturing costs
- Summary
- Abstract
- Description
- Claims
- Application Information
AI Technical Summary
Problems solved by technology
Method used
Examples
Embodiment 1
[0015] At the entrance of one end of the tubular bed, 100 kg of crushed waste plastics below 20 cm and 2.2 kg of catalyst powder will pass through the hopper with stirring, and the materials will be fed continuously and evenly while mixing, driven by the built-in near-wall scraper in the tubular bed. Under the condition, the material moves slowly from the front section of the tube bed low-temperature dehydration to the high-temperature cracking section. The waste plastics are dehydrated at 160-220°C, and then the waste plastics are cracked at 360-390°C. The moving speed of the materials is adjusted to ensure that the waste plastics The cracking is fully and completely, and 82.4 kg of crude oil is produced in the cracking process, and the yield is 82.4% based on waste plastics. The crude oil is heated and vaporized into the secondary catalytic cracking and upgrading fluidized bed reactor, at a temperature of 390-400°C, a pressure of 1.8bar, and a catalytic reaction space velocit...
Embodiment 2
[0017] At the entrance of one end of the tubular bed, 200 kg of crushed waste plastics and 3 kg (equivalent to 100:1.5 weight ratio) of catalyst powder are continuously mixed and fed, and the waste plastics are dehydrated at 150-210 ° C, and then at 370- Waste plastics are pyrolyzed at a temperature of 390°C. During this pyrolysis process, 81.3 kg of crude oil is produced, and the yield of crude oil is 81.3% based on waste plastics. The crude oil is heated and vaporized into the secondary catalytic cracking and upgrading fluidized bed reactor, at a temperature of 380-390°C, a pressure of 3.1bar, and a catalytic reaction space velocity WHSV of 0.50h -1 Under the condition of catalytic cracking, the yield of the obtained gasoline and diesel fraction relative to the crude oil is 82.5%.
Embodiment 3
[0019] At the entrance of one end of the tubular bed, 150 kg of crushed waste plastics and 3.9 kg (equivalent to 100:2.6 weight ratio) of catalyst powder are continuously mixed and fed, and the waste plastics are dehydrated at 180-250 ° C, followed by 360- Waste plastics are pyrolyzed at a temperature of 390°C. During this pyrolysis process, 81.5 kg of crude oil is produced, and the yield of crude oil is 81.5% based on waste plastics. The crude oil is heated and vaporized into the secondary catalytic cracking and upgrading fluidized bed reactor, at a temperature of 382-398°C, a pressure of 2.5bar, and a catalytic reaction space velocity WHSV of 1.0h -1 Under the condition of catalytic cracking, the yield of the obtained gasoline and diesel fraction relative to the crude oil is 84.9%.
PUM
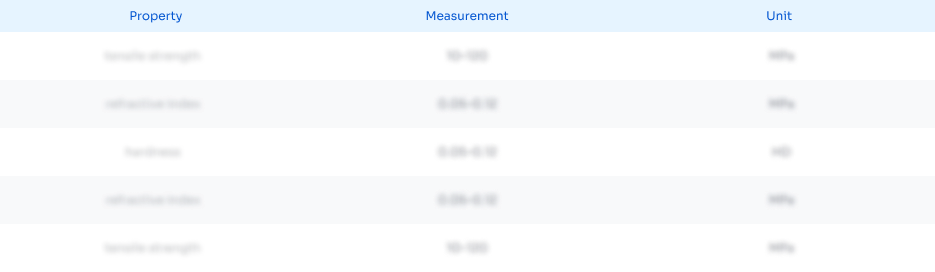
Abstract
Description
Claims
Application Information

- R&D
- Intellectual Property
- Life Sciences
- Materials
- Tech Scout
- Unparalleled Data Quality
- Higher Quality Content
- 60% Fewer Hallucinations
Browse by: Latest US Patents, China's latest patents, Technical Efficacy Thesaurus, Application Domain, Technology Topic, Popular Technical Reports.
© 2025 PatSnap. All rights reserved.Legal|Privacy policy|Modern Slavery Act Transparency Statement|Sitemap|About US| Contact US: help@patsnap.com