Wear-resistant rocking bed face putty layer material
A putty layer and wear-resistant filler technology, applied in the field of surface wear-resistant coatings, can solve the problems of allergies, wear resistance decline, short service life, etc. expensive effect
- Summary
- Abstract
- Description
- Claims
- Application Information
AI Technical Summary
Problems solved by technology
Method used
Examples
Embodiment 1
[0011] As a putty on the surface of the beneficiation shaker. Firstly, the commonly used fillers are fully and effectively mixed according to quartz sand: talc powder: cast stone powder: silicon carbide = 2:1:0.5:0.05, and then the synthetic resin, curing agent and catalyst are in a reasonable ratio of 1:0.03: 0.01 and stir evenly, then mix the filler and resin and stir evenly, and then manually batch the ash on the surface of the shaker. Generally, one layer of ash can reach the thickness of 8-10 layers of ash for raw lacquer ash. After curing, remove the flash, and then Check the flatness of the surface of the shaking table, and apply ash filling process for the places that do not meet the requirements, until the flatness of the entire surface of the shaking table meets the technical requirements, then smooth the surface of the table, and finally nail the required strips, rinse Just finish the topcoat. Its basic operation process is similar to that of the raw lacquer shaker...
Embodiment 2
[0013] Surface decoration of mechanical equipment. Clean up the welding part of the equipment and other parts that need to be decorated first, remove the metal rust and oil that are easy to fall off, and then use this filler to scrape and fill repeatedly. The ratio is: resin: curing agent: catalyst: quartz sand: Talc powder: cast stone powder: silicon carbide = 1: 0.05: 0.02: 2: 1.2: 0.5: 0.02, after the putty is solidified, it can be polished with emery cloth, and finally paint is applied according to the product coating requirements.
Embodiment 3
[0015] As a surface lining for environmental protection and wear-resistant equipment. First, derust and remove scale on the surface of the equipment. Shot blasting or sandblasting can be used to make the parts of the equipment that need to be pasted and lined rougher, so as to enhance the adhesion of the filler to the surface of the equipment, and then rinse a layer first. The ratio of the thinner putty ash is: resin: curing agent: catalyst: quartz sand: talcum powder: cast stone powder: silicon carbide = 1.2: 0.06: 0.03: 1.8: 1: 0.5: 0.05, and then mount the glass The fiber cloth is soaked with the resin prepared with curing agent and catalyst (the ratio is: resin: curing agent: catalyst = 1: 6%: 3%). After curing, the surface is slightly flattened and then the second layer of pasting is carried out, and so on. Operate until the specified thickness of the product's anti-corrosion layer is reached.
PUM
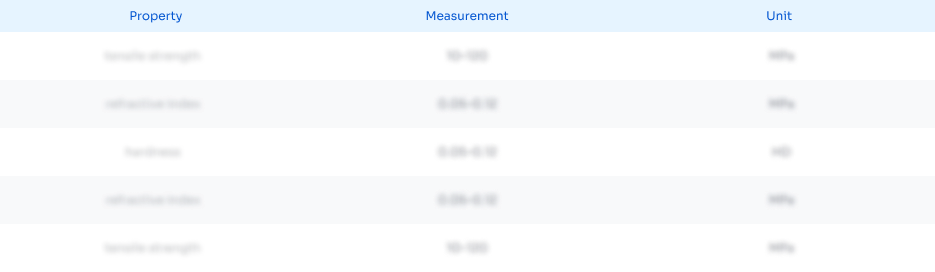
Abstract
Description
Claims
Application Information

- R&D
- Intellectual Property
- Life Sciences
- Materials
- Tech Scout
- Unparalleled Data Quality
- Higher Quality Content
- 60% Fewer Hallucinations
Browse by: Latest US Patents, China's latest patents, Technical Efficacy Thesaurus, Application Domain, Technology Topic, Popular Technical Reports.
© 2025 PatSnap. All rights reserved.Legal|Privacy policy|Modern Slavery Act Transparency Statement|Sitemap|About US| Contact US: help@patsnap.com