Method for manufacturing wafer-stage glass micro-cavity
A manufacturing method and glass microtechnology, applied in the field of MEMS manufacturing, can solve the problems of high cost, inability to precisely control the size of the microcavity, low efficiency, etc., and achieve the effects of good airtightness, high bonding strength and low roughness
- Summary
- Abstract
- Description
- Claims
- Application Information
AI Technical Summary
Problems solved by technology
Method used
Image
Examples
Embodiment 1
[0024] A method for manufacturing a wafer-level glass microcavity, comprising the following steps:
[0025] In the first step, a specific pattern is formed on a Si wafer (such as a 4-inch wafer) by etching using a Si micromachining process, and the micromachining process of the pattern structure on the Si original wafer is a wet etching process or a dry inductively coupled plasma One of the bulk (ICP) etching process, reactive ion etching or deep reactive ion etching, the pattern can be a square or circular groove array, or a number of different graphics, (in fact, three-dimensionally, To engrave a specific pattern is to engrave a groove on a silicon wafer, and it is a pattern in two dimensions)
[0026] In the second step, the above-mentioned Si wafer and the Pyrex7740 glass wafer (a brand of borosilicate glass, produced by Corning-corning Company in the United States, available in the market, usually polished, and its size is the same as the Si wafer) in less than Bonding i...
Embodiment 2
[0031] A method for manufacturing a wafer-level glass microcavity, comprising the following steps:
[0032] The first step is to etch a specific pattern on a 4-inch Si wafer by using deep reactive ion etching (in fact, in three dimensions, it is a groove on the silicon wafer, and in two dimensions, it is a pattern). The pattern is a square groove array , the aspect ratio of the pattern is 20:1, the silicon wafer is polished,
[0033] In the second step, the above-mentioned Si wafer and (4 inches) Pyrex7740 glass wafer of the same size (a kind of brand of borosilicate glass, produced by Corning-corning Company in the United States, available in the market, have been polished) at 0.5Pa The bonding is carried out under the atmosphere, and the bonding is carried out on the EVG-501 anode bonding machine, so that the above-mentioned specific pattern on the Pyrex7740 glass forms a sealed cavity, and the bonding surface is routinely cleaned and polished according to the requirements o...
PUM
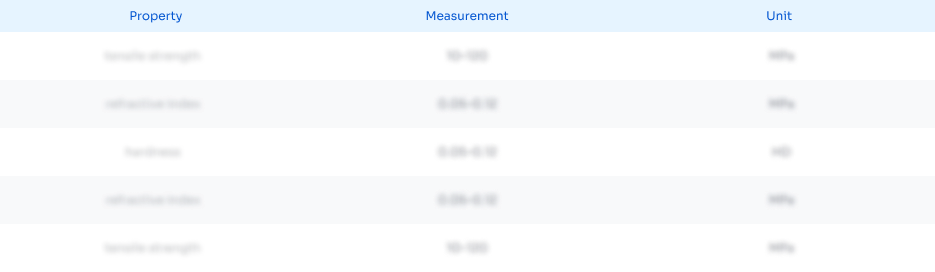
Abstract
Description
Claims
Application Information

- R&D
- Intellectual Property
- Life Sciences
- Materials
- Tech Scout
- Unparalleled Data Quality
- Higher Quality Content
- 60% Fewer Hallucinations
Browse by: Latest US Patents, China's latest patents, Technical Efficacy Thesaurus, Application Domain, Technology Topic, Popular Technical Reports.
© 2025 PatSnap. All rights reserved.Legal|Privacy policy|Modern Slavery Act Transparency Statement|Sitemap|About US| Contact US: help@patsnap.com