Coarse and precision composite processing method suitable for numerical control electrospark wire-electrode cutting
A compound machining and EDM technology, which is applied in the field of workpiece processing, can solve the problems of affecting the processing speed, surface quality and processing accuracy of medium processing and finishing processing, reducing cutting speed, processing accuracy and surface quality, and generating jitter, etc. It achieves the effects of convenient operation, improved processing speed and high control precision.
- Summary
- Abstract
- Description
- Claims
- Application Information
AI Technical Summary
Problems solved by technology
Method used
Image
Examples
Embodiment Construction
[0028] The present invention will be further described in detail below in conjunction with the accompanying drawings.
[0029] The present invention is a coarse, medium and fine composite machining method suitable for numerical control electric discharge wire cutting. The method completes three different machining standards of coarse, medium and fine in one feeding process, and uses online real-time detection of machining gap changes to control The machining standards are converted, and the electrode wire is fed one step after the finishing requirements are met, and the next rough, medium and finishing standards are completed again, so as to reciprocate.
[0030] The processing steps of the rough, medium and fine composite processing method of the present invention are: the roughing standard, the intermediate processing standard and the finishing standard are set according to the pulse voltage and current parameters output by the pulse power supply; then it is detected by the serv...
PUM
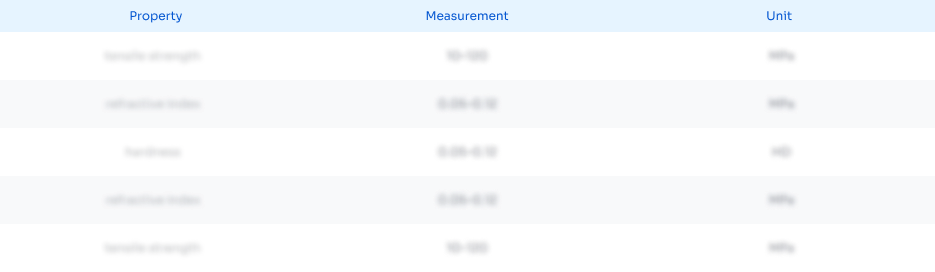
Abstract
Description
Claims
Application Information

- R&D
- Intellectual Property
- Life Sciences
- Materials
- Tech Scout
- Unparalleled Data Quality
- Higher Quality Content
- 60% Fewer Hallucinations
Browse by: Latest US Patents, China's latest patents, Technical Efficacy Thesaurus, Application Domain, Technology Topic, Popular Technical Reports.
© 2025 PatSnap. All rights reserved.Legal|Privacy policy|Modern Slavery Act Transparency Statement|Sitemap|About US| Contact US: help@patsnap.com