In-situ consolidation fibre laying method and device for producing resin-based compound material component
A composite material component and manufacturing method technology, applied in the field of in-situ consolidation fiber placement, can solve the problems of complex structure, inability to manufacture negative curvature surface components and non-revolving components, lack of flexibility, etc., and achieve reasonable cost , Simple structure, cost reduction effect
- Summary
- Abstract
- Description
- Claims
- Application Information
AI Technical Summary
Problems solved by technology
Method used
Image
Examples
specific Embodiment approach 1
[0029] combine figure 1 This embodiment will be described. This embodiment is a specific manufacturing system, and its working process is as follows: firstly, a CAD model is designed according to the functional requirements of the product, which can be realized by using three-dimensional design software such as Pro / E. According to the use environment of the product, use CAE software such as ANSYS to simulate and analyze its working conditions. The fiber laying path is planned according to the analysis results, and the planned path is realized by robot control instructions. Then, with the assistance of other equipment and devices, the laying components are manufactured, and finally the manufactured laying components are subjected to secondary processing, such as mechanical processing, to finally produce finished products.
specific Embodiment approach 2
[0030] combine figure 2 , image 3 This embodiment will be described. This embodiment is a laying and in-situ radiation curing mechanism installed at the end of the robot. It includes an in-situ radiation curing source device 5-1, a laying head 5-2, a pressing mechanism 5-3, a connection installation mechanism 5-4, and the manufacturing of the laying head 5-2 is made according to conventional mechanical design or refers to a patent Application 200610010438.3 made. The pressing mechanism is made up of pressing roller or pressing shoe 5-3-1 and pressing cylinder 5-3-2. The pressure roller or the pressure shoe is connected to the piston of the cylinder, and the cylinder pushes the pressure roller or the pressure shoe to apply the pressing force on the fiber layer a to be cured. By adjusting the air pressure of the cylinder, the fiber layer a to be cured is the same as the layer a The cured fiber lay-up b is tightly closed, keeping the compaction force constant and the compac...
Embodiment approach 3
[0032] This embodiment combines figure 2 , image 3 , Figure 4 , Figure 5This embodiment will be described. This embodiment is a complete manufacturing system. Used to manufacture rotary type fiber composite components. It includes a rotary mandrel supporting positioning mechanism 1-1, a robot 2-1, a laying head 5-2, a pressing mechanism 5-3, a fiber frame 3-1, a fiber soaking device 3-2, and a tensioning device 3-3 , fiber carding conveying device 3-4, fiber bundle 3-5; control cabinet 4-1, air compressor 4-2, resin pump 4-3, radiation curing device 5-1 and other parts. Under the control of the control cabinet 4-1, the fiber bundle 3-5 passes through the fiber soaking device 3-2, the tensioning device 3-3, the fiber carding and conveying device 3-4 from the fiber rack 3-1 to the laying head 5- 2. Under the action of the laying head, the fiber bundle soaked in resin is laid on the surface of the core mold 1-1-3 supported by the core mold frame 1-1 under the action of ...
PUM
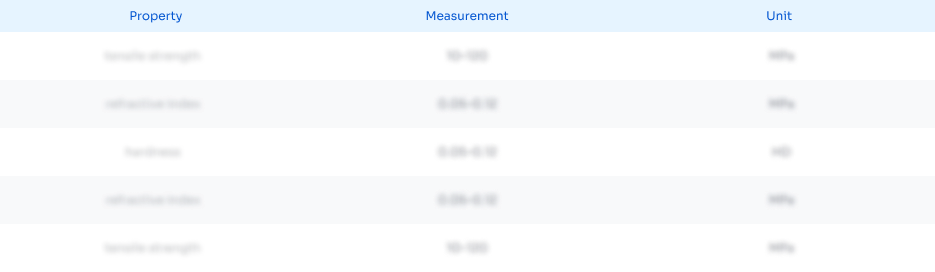
Abstract
Description
Claims
Application Information

- Generate Ideas
- Intellectual Property
- Life Sciences
- Materials
- Tech Scout
- Unparalleled Data Quality
- Higher Quality Content
- 60% Fewer Hallucinations
Browse by: Latest US Patents, China's latest patents, Technical Efficacy Thesaurus, Application Domain, Technology Topic, Popular Technical Reports.
© 2025 PatSnap. All rights reserved.Legal|Privacy policy|Modern Slavery Act Transparency Statement|Sitemap|About US| Contact US: help@patsnap.com