Casting technique of casting roll surface nano modification
A nano-modification and casting process technology, applied in the field of roll casting process, can solve the problems of low roll strength, hardness, thermal fatigue strength, complex heat treatment process, secondary pollution of alloys, etc., to simplify the heat treatment process and the process method. Controlled, high-purity effects
- Summary
- Abstract
- Description
- Claims
- Application Information
AI Technical Summary
Problems solved by technology
Method used
Examples
Embodiment 1
[0008] Will AL 2 o 3 Nanomaterials and Zircon Powder, by AL 2 o 3 Nano material: zircon powder = 1: 10 batching, grind for 15 minutes with a roller compactor for casting to make nano coating powder for casting, add denatured alcohol to blend into 0.08Kg / liter casting coating, spray or brush the coating on On the surface of the mold, the molten steel is filled into the mold to make a casting roll.
Embodiment 2
[0010] Will AL 2 o 3 Nanomaterials and Bauxite Powders, by AL 2 o 3 Nano material: bauxite powder=1.2: 10 batching, grind 12 minutes with roller compactor for casting, make the nano-coating powder for casting, add water and mix and blend into 0.1Kg / liter casting coating, coating is sprayed or brushed on On the surface of the mold, the molten steel is filled into the mold to make a casting roll.
[0011] The casting roll made by the present invention is applied to the roller table equipment of the second phase production line of Xiangtan Iron and Steel Company. During inspection, the surface hardness of the casting roll on the roll table equipment is 30% higher than that of the first phase roll. The service life of the rolls in the first phase is increased by 60% compared with the first phase.
PUM
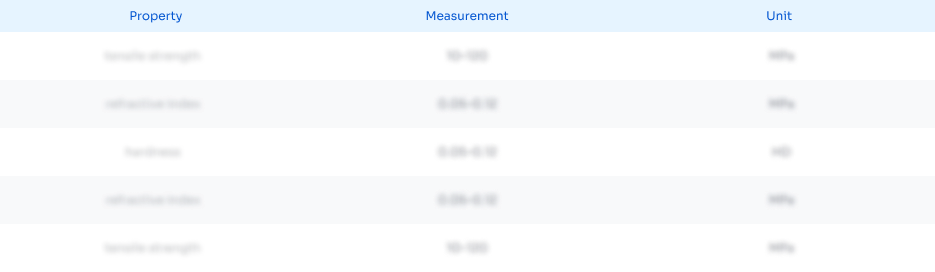
Abstract
Description
Claims
Application Information

- Generate Ideas
- Intellectual Property
- Life Sciences
- Materials
- Tech Scout
- Unparalleled Data Quality
- Higher Quality Content
- 60% Fewer Hallucinations
Browse by: Latest US Patents, China's latest patents, Technical Efficacy Thesaurus, Application Domain, Technology Topic, Popular Technical Reports.
© 2025 PatSnap. All rights reserved.Legal|Privacy policy|Modern Slavery Act Transparency Statement|Sitemap|About US| Contact US: help@patsnap.com