Glass-fluorine complex fire resistant filter material and method for manufacturing same
A technology of filter material and manufacturing method, which is applied in the field of high-temperature-resistant composite filter material and its manufacturing, can solve the problems of non-stickiness of polytetrafluoroethylene, blockage of filter material pores, poor high-temperature resistance, etc., and achieve easy dust removal , Stable structure, good anti-oxidation effect
- Summary
- Abstract
- Description
- Claims
- Application Information
AI Technical Summary
Problems solved by technology
Method used
Examples
Embodiment 1
[0027] Use neutral glass fiber woven cloth (450 grams per square meter), and polytetrafluoroethylene fiber nets that have been opened, mixed, and carded to form a net, and laminated together, and composited with spunlace. together. Dipping and rolling with polytetrafluoroethylene emulsion to make the amount of liquid to be 80%, and then drying and setting at 125°C.
[0028] The specification of the obtained glass-fluorine composite high-temperature-resistant filter material is 500 grams per square meter, the maximum use temperature is 300°C, and the long-term use temperature is 260°C. Strength: radial 1000 (N / 2.5cm), weft 800 (N / 2.5cm). The filtration efficiency is 97.83%, the filtration resistance is 19.33Pa, and the wear times are 929 times.
Embodiment 2
[0030] Alkaline glass fiber woven cloth (490 grams per square meter) is laminated with polytetrafluoroethylene fiber nets that have been opened, mixed, and carded into a net, and they are composited using a spunlace process. together. Dipping and rolling with polytetrafluoroethylene emulsion to make the amount of liquid taken up to 150%, and then drying and setting at 175°C.
[0031] The specification of the obtained glass-fluorine composite high-temperature-resistant filter material is 550 grams per square meter, the maximum use temperature is 300°C, and the long-term use temperature is 260°C. Strength: radial 1100 (N / 2.5cm), latitude 900 (N / 2.5cm), filtration efficiency 92.12%, filtration resistance 20.48Pa, abrasion resistance 931 times.
Embodiment 3
[0033] Alkaline glass fiber woven cloth (400 grams per square meter) is laminated with polytetrafluoroethylene fiber nets that have been opened, mixed, and carded into a net, and they are composited using a spunlace process. together. Dipping and rolling with polytetrafluoroethylene emulsion to make the amount of liquid to be 60%, then drying and setting at 200°C.
[0034] The obtained glass-fluorine composite high-temperature-resistant filter material has a specification of 510 grams per square meter, a maximum service temperature of 300°C, and a long-term use temperature of 260°C. Intensity: radial 1000 (N / 2.5cm), weft 820 (N / 2.5cm), filtration efficiency 89.54%, filtration resistance 18.45Pa, abrasion resistance 911 times.
PUM
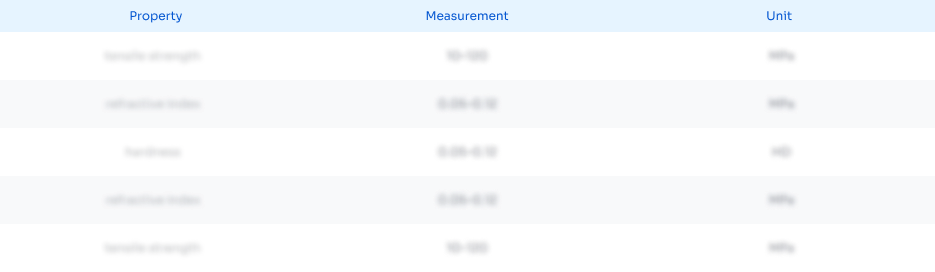
Abstract
Description
Claims
Application Information

- R&D Engineer
- R&D Manager
- IP Professional
- Industry Leading Data Capabilities
- Powerful AI technology
- Patent DNA Extraction
Browse by: Latest US Patents, China's latest patents, Technical Efficacy Thesaurus, Application Domain, Technology Topic, Popular Technical Reports.
© 2024 PatSnap. All rights reserved.Legal|Privacy policy|Modern Slavery Act Transparency Statement|Sitemap|About US| Contact US: help@patsnap.com