Ultrasonic vibration and welding stick feeding system compound welding method and device thereof
An ultrasonic vibration and welding device technology, applied in welding equipment, arc welding equipment, manufacturing tools, etc., can solve the problems of energy enhancement, low ultrasonic vibration efficiency, etc., to improve the crystallization state, improve the energy distribution of the molten pool, and improve the stability. Effect
- Summary
- Abstract
- Description
- Claims
- Application Information
AI Technical Summary
Problems solved by technology
Method used
Image
Examples
Embodiment 1
[0018] Embodiment 1, in conjunction with Fig. 1, the welding method of described supersonic wave and non-MIG arc welding welding wire feeding system compound, at first will redesign ultrasonic transducer 1 and ultrasonic horn 2, make it conform to welding wire feeding Into the complex requirements of the system. Accurately calculate the ultrasonic horn 2 to find the required node positions; reasonably combine the wire feeder 3 used for welding with the horn 2 so that the ultrasonic wave can be effectively transmitted to the welding wire 5; during welding, the arc After the start is stable, start the welding wire feeding system 4 and start the ultrasonic power supply to load the electrical signal to the ultrasonic transducer 1, convert the electrical energy into vibration through the transducer 1, amplify the ultrasonic vibration amplitude through the horn 2, and finally transmit Give wire 5.
Embodiment 2
[0019] Embodiment 2: in conjunction with Fig. 1, described a kind of welding method and its device of ultrasonic vibration and welding wire feeding system combination, the electric signal of ultrasonic power supply is converted into mechanical vibration by transducer 1, because the mechanical vibration of transducer The amplitude is small, and the horn is used to amplify it to 20μm-200μm, and finally the vibration is transmitted to the wire feed nozzle 3 embedded in the end of the horn. The above device can work under ultrasonic vibration with a frequency of 1 kHz to 2 MHz. The input power of ultrasound can be adjusted arbitrarily between 1W and 1000W. Welding is carried out according to the method of common non-melting electrode gas shielded welding. After applying ultrasound, the welding wire 5 will be subjected to the action of ultrasound, and the molten droplet will be affected by ultrasonic vibration, which helps to control the shape and size of the molten droplet during ...
Embodiment 3
[0020] Embodiment 3: in conjunction with Fig. 1, on the basis of the welding method described above, the ultrasonic vibration energy is transmitted to the welding wire 5, so that after the ordinary non-melting electrode gas shielded welding is applied with ultrasonic waves, the transition of the welding wire 5 droplet is obvious The improvement is more conducive to the transfer of droplets. In the case of small current, the size of the droplet transfer can be controlled; and the qualitative and quantitative control of the droplet transfer can be realized. On the basis of the common non-melting electrode arc welding system, the welding torch used in welding is not changed, only the ultrasonic wave is applied to the welding wire 5, and then transmitted to the molten droplet and molten pool. The method improves the efficiency of the welding arc and realizes the transformation of the traditional welding system. The ultrasonic waves transmitted through the welding wire 5 have an e...
PUM
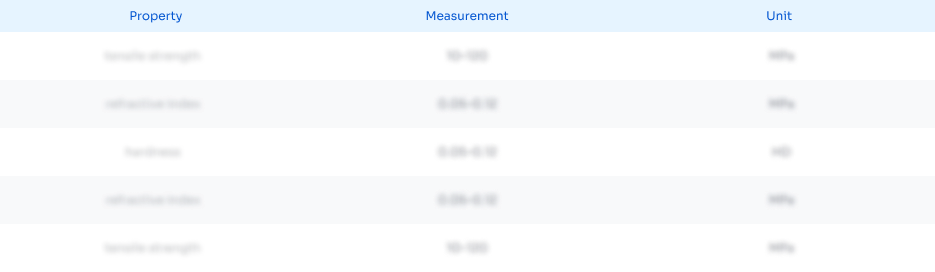
Abstract
Description
Claims
Application Information

- R&D Engineer
- R&D Manager
- IP Professional
- Industry Leading Data Capabilities
- Powerful AI technology
- Patent DNA Extraction
Browse by: Latest US Patents, China's latest patents, Technical Efficacy Thesaurus, Application Domain, Technology Topic, Popular Technical Reports.
© 2024 PatSnap. All rights reserved.Legal|Privacy policy|Modern Slavery Act Transparency Statement|Sitemap|About US| Contact US: help@patsnap.com