Environmental protection halogen-free anti-flaming polypropylene composite material and preparation method thereof
A flame retardant polypropylene and composite material technology, applied in the field of flame retardant composite materials, can solve the problems of material mechanical properties decline and inability to process, achieve the effect of small smoke generation, excellent flame retardant performance, and solve potential harm
- Summary
- Abstract
- Description
- Claims
- Application Information
AI Technical Summary
Problems solved by technology
Method used
Examples
Embodiment 1
[0023] Accurately weigh 100 parts by weight of polypropylene powder, 30 parts by weight of magnesium hydroxide, 3 parts by weight of red phosphorus, 10 parts by weight of MBS, 20 parts by weight of PP-g-MAH, antioxidant (2,4-di-tert-butyl 0.2 parts by weight of phenyl) tricarbonate and a small amount of lubricant white oil are stirred in a high-speed mixer for two minutes; the premix is melt-extruded on a twin-screw extruder, cooled, pelletized, dried, and injected. Nine temperature intervals of the extruder: the first interval is 175°C, the second interval is 180°C, the third interval is 189°C, the fourth interval is 197°C, the fifth interval is 201°C, the sixth interval is 201°C, the seventh interval is 202°C, the eighth interval is 205°C, and the ninth interval 205°C, the host speed is 22r / min. The pellets were molded into the desired test specimens in an injection molding machine. Determination of flame retardancy and mechanical properties of flame retardant materials. ...
Embodiment 2
[0025] Accurately weigh 100 parts by weight of polypropylene powder, 40 parts by weight of magnesium hydroxide, 3 parts by weight of red phosphorus, 10 parts by weight of MBS, 20 parts by weight of PP-g-MAH, antioxidant (2,4-di-tert-butyl 0.2 parts by weight of phenyl) tricarbonate and a small amount of lubricant white oil are stirred in a high-speed mixer for two minutes; the premix is melt-extruded on a twin-screw extruder, cooled, pelletized, dried, and injected. Nine temperature intervals of the extruder: the first interval is 175°C, the second interval is 180°C, the third interval is 189°C, the fourth interval is 197°C, the fifth interval is 201°C, the sixth interval is 201°C, the seventh interval is 202°C, the eighth interval is 205°C, and the ninth interval 205°C, the host speed is 22r / min. The pellets were molded into the desired test specimens in an injection molding machine. Determination of flame retardancy and mechanical properties of flame retardant materials. ...
Embodiment 3
[0027] Accurately weigh 100 parts by weight of polypropylene powder, 50 parts by weight of magnesium hydroxide, 3 parts by weight of red phosphorus, 10 parts by weight of MBS, 20 parts by weight of PP-g-MAH, antioxidant (2,4-di-tert-butyl 0.2 parts by weight of phenyl) tricarbonate and a small amount of lubricant white oil are stirred in a high-speed mixer for two minutes; the premix is melt-extruded on a twin-screw extruder, cooled, pelletized, dried, and injected. Nine temperature intervals of the extruder: the first interval is 175°C, the second interval is 180°C, the third interval is 189°C, the fourth interval is 197°C, the fifth interval is 201°C, the sixth interval is 201°C, the seventh interval is 202°C, the eighth interval is 205°C, and the ninth interval 205°C, the host speed is 22r / min. The pellets were molded into the desired test specimens in an injection molding machine. Determination of flame retardancy and mechanical properties of flame retardant materials. ...
PUM
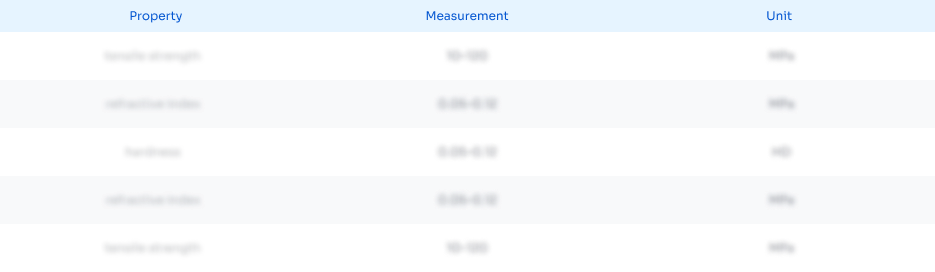
Abstract
Description
Claims
Application Information

- Generate Ideas
- Intellectual Property
- Life Sciences
- Materials
- Tech Scout
- Unparalleled Data Quality
- Higher Quality Content
- 60% Fewer Hallucinations
Browse by: Latest US Patents, China's latest patents, Technical Efficacy Thesaurus, Application Domain, Technology Topic, Popular Technical Reports.
© 2025 PatSnap. All rights reserved.Legal|Privacy policy|Modern Slavery Act Transparency Statement|Sitemap|About US| Contact US: help@patsnap.com