Multi-fluid composite electrostatic spinning device
An electrospinning and multi-fluid technology, which is applied in textiles and papermaking, filament/thread forming, fiber processing, etc., can solve problems such as limitations, and achieve the effect of a wide range of applicable materials, simple devices, and broad application prospects
- Summary
- Abstract
- Description
- Claims
- Application Information
AI Technical Summary
Problems solved by technology
Method used
Image
Examples
Embodiment 1
[0032] See Figure 1~3 . A multi-fluid composite electrospinning spinneret 1 installed on the base 15 is composed of a large-diameter outer nozzle 19 and 4 small-diameter inner nozzles 13 embedded in the outer nozzle, and is made of conductive metal. The inner and outer nozzles are respectively connected to the positive high voltage or negative high voltage output from one end of a high-voltage power supply 2 with a power supply of 0-100kV through separate wires connected to the nozzle; in front of the multi-fluid composite electrospinning spinneret 1 A conductive flat metal fiber collector 3 that can move in parallel is installed at a distance of 5-50 cm. The electric field strength between the multi-fluid composite electrospinning spinneret and the fiber collector is 0.5-3.0 kV / cm; the fiber collector 3 passes through the wire Connect with the ground wire of the other end of the high-voltage power supply 2 to ensure zero potential of the fiber collector.
[0033] The inlet...
Embodiment 2
[0044] Preparation of multi-channel organic and polymeric micro- and nanotubes: the high polymer solution is used as the outer layer spinning solution, the oil immiscible with the outer layer liquid is used as the inner layer fluid, and through the device of the present invention as in Example 1, Then the product is washed to remove oil to obtain micro and nanotubes with multi-channel structure.
[0045] For example, the preparation process of two-channel acrylic fiber hollow micro and nanofibers is: dissolve 2.0g polyacrylonitrile (PAN) in 8.0g N, N-dimethylformamide (DMF), stir until completely dissolved to form a stable and uniform solution , the solution is delivered to the outer spray pipe through a liquid supply pump and a conduit; liquid paraffin (or vegetable oil, machine oil, etc.) is used as an inner layer fluid, and is delivered to two inner spray pipes through a liquid supply pump and a conduit. The composite spinneret is connected to a high-voltage positive electr...
Embodiment 3
[0048] Preparation of multi-component core-shell structure inorganic micro- and nanofibers: use the mixed solution of inorganic sol and polymer as the outer layer spinning liquid, and use the required multi-component functional materials as the inner layer fluid according to the actual situation, and pass through as in the example 1, an inorganic functional fiber material with a multi-core-shell structure is obtained.
[0049] Such as tin dioxide SnO 2 , indium oxide In 2 o 3 , zinc oxide ZnO triple core, titanium dioxide TiO 2 The preparation process of shell composite structure nanofibers is: dissolve 2.0g polyvinylpyrrolidone (PVP) in 10.0g absolute ethanol and 1.0g glacial acetic acid, stir until completely dissolved, then continue to stir and add 6.0g tetrabutyl titanate (or isopropanol titanate), and continue stirring for 1 hour to form a stable and uniform titanium sol solution. The solution is delivered to the outer spray pipe through the liquid supply pump and the...
PUM
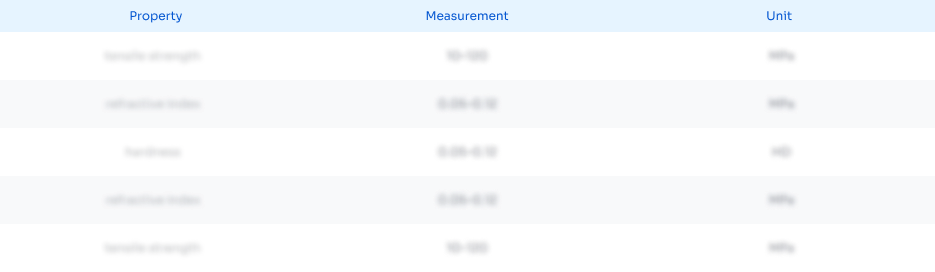
Abstract
Description
Claims
Application Information

- R&D Engineer
- R&D Manager
- IP Professional
- Industry Leading Data Capabilities
- Powerful AI technology
- Patent DNA Extraction
Browse by: Latest US Patents, China's latest patents, Technical Efficacy Thesaurus, Application Domain, Technology Topic, Popular Technical Reports.
© 2024 PatSnap. All rights reserved.Legal|Privacy policy|Modern Slavery Act Transparency Statement|Sitemap|About US| Contact US: help@patsnap.com