Double-layer composite production method for plastic film sheet material on blowfilm machine and equipment thereof
A plastic film, double-layer composite technology, applied in the direction of flat products, other household appliances, household appliances, etc., can solve the problems of easy bending and breaking of blades and tool holders, increase production costs, high equipment prices, etc., and save machine consumption. , the effect of increasing softness and reducing production costs
- Summary
- Abstract
- Description
- Claims
- Application Information
AI Technical Summary
Problems solved by technology
Method used
Image
Examples
Embodiment 1
[0016] Embodiment 1, a kind of plastic film sheet, its raw material formula is the copolymer (EVA) 9.5 kilograms of low-density polyethylene (LDPE) 0.5 kilograms, ethylene / vinyl acetate, and the copolymer of ethylene / vinyl acetate is in order to increase The stickiness and softness of the sheet material production process can be increased or decreased according to the specific situation. The production method is to double-layer compound on the blown film machine, mix the raw materials and place them in a special blow molding machine, and the die head temperature of the blow molding machine is 150-170 degrees, compact and roll the blown barrel-shaped plastic film into bundles.
Embodiment 2
[0017] Embodiment 2, a kind of plastic film sheet, its raw material formula is 2 kilograms of low-density polyethylene (LDPE), 8 kilograms of the copolymer (EVA) of ethylene / vinyl acetate, and its preparation method is double-layer composite on blown film machine , Mix the raw materials and place them in a special blow molding machine. The temperature of the die head of the blow molding machine is 150-170 degrees, and the plastic film in the shape of a blown barrel is compacted and rolled into bundles.
Embodiment 3
[0018] Embodiment 3, a kind of plastic film sheet, its raw material formula is 6.5 kilograms of low-density polyethylene (LDPE), 3.5 kilograms of the copolymer (EVA) of ethylene / vinyl acetate, and its preparation method is double-layer composite on blown film machine , Mix the raw materials and place them in a special blow molding machine. The temperature of the die head of the blow molding machine is 150-170 degrees, and the plastic film in the shape of a blown barrel is compacted and rolled into bundles.
[0019] Fig. 2 is a schematic structural diagram of the principle of Embodiment 1 of the special equipment of the present invention. On the basis of the existing blow molding machine, the tool holder system 7, one winding roller 8 and two nip rollers 64 are canceled, and only one winding roller 8 is retained. Turn down the gap between the two rollers of traction roller 6, and the size of the concrete gap is determined by the thickness of the required plastic sheet. That is,...
PUM
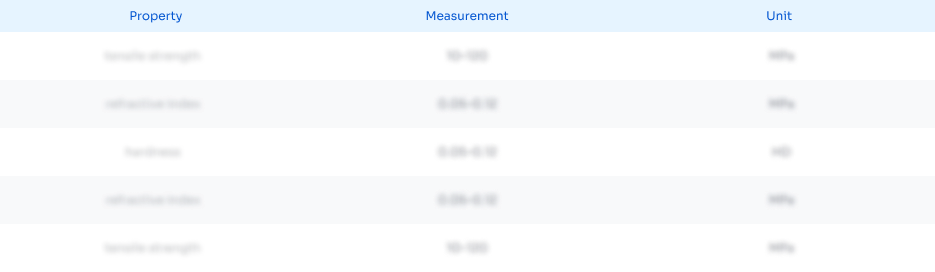
Abstract
Description
Claims
Application Information

- R&D
- Intellectual Property
- Life Sciences
- Materials
- Tech Scout
- Unparalleled Data Quality
- Higher Quality Content
- 60% Fewer Hallucinations
Browse by: Latest US Patents, China's latest patents, Technical Efficacy Thesaurus, Application Domain, Technology Topic, Popular Technical Reports.
© 2025 PatSnap. All rights reserved.Legal|Privacy policy|Modern Slavery Act Transparency Statement|Sitemap|About US| Contact US: help@patsnap.com