Manufacturing process for low-temperature shaped elastic coating yarn
A low-temperature setting and manufacturing process technology, which is applied in textiles and papermaking, heating/cooling fabrics, fabric surface trimming, etc., can solve the problems of low strength of XLA elastic filament fibers, different wrapping and compounding processing techniques, and small resilience. Achieve good fabric post-treatment characteristics and use properties, overcome high setting temperature and stable width
- Summary
- Abstract
- Description
- Claims
- Application Information
AI Technical Summary
Problems solved by technology
Method used
Image
Examples
Embodiment 1
[0023] Example 1: DOW XLA elastic fiber is used as polyolefin-based elastic fiber as the core material, which is produced by Dow Chemical Company in the United States, and bamboo fiber / silk 40 / 60, 120N / z is used as the covering material. The cake-shaped DOW XLA elastic yarn bobbin 2 is driven by the feeding roller 1 to actively retreat. After passing through the pre-drawing roller 3, the draft ratio is 2.0 and the draft tension is 2CN, and it is fed into the hollow spindle 5. When the DOW XLA elastic yarn is drawn out from the hollow spindle rod, the hollow spindle rotates at high speed under the friction of the dragon belt 4, so that the outer covering silk (yarn) 6 on the double-sided bobbin 7 on the spindle rotates at a high speed and retreats. , under the action of the balloon guide wire hook 8, the outer covering wire forms a covering balloon. As soon as the covering balloon turns around the axis of the spindle, a twist is added to the outer covering wire, and the coverin...
Embodiment 2
[0024] Embodiment 2: DOW XLA elastic fiber is used as polyolefin-based elastic fiber as the material, which is produced by Dow Chemical Company in the United States. Different coating materials are selected. Under different processing conditions, the setting temperature is 60 ° C. The drawing tension is 3CN, the winding speed is 8.5m / min, and the winding tension is 15CN, and the steps carried out in Example 1 are carried out to obtain the following table:
[0025]
[0026] Polyester (DTY) / 75D+XLA / 40D
Embodiment 3
[0027] Embodiment 3: DOW XLA elastic fiber is used as polyolefin-based elastic fiber as the material, which is produced by Dow Chemical Company in the United States. Different coating materials are selected. Under different processing conditions, the setting temperature is 80 ° C. The drawing tension is 5CN, the winding speed is 9.5m / min, and the winding tension is 20CN, and the steps carried out in Example 1 are carried out to obtain the following table:
[0028]
[0029] Polyester / cotton 50 / 50, 40s+XLA / 40D
PUM
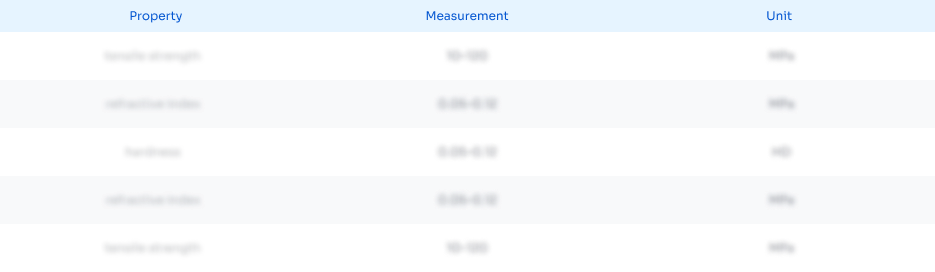
Abstract
Description
Claims
Application Information

- R&D
- Intellectual Property
- Life Sciences
- Materials
- Tech Scout
- Unparalleled Data Quality
- Higher Quality Content
- 60% Fewer Hallucinations
Browse by: Latest US Patents, China's latest patents, Technical Efficacy Thesaurus, Application Domain, Technology Topic, Popular Technical Reports.
© 2025 PatSnap. All rights reserved.Legal|Privacy policy|Modern Slavery Act Transparency Statement|Sitemap|About US| Contact US: help@patsnap.com