Composite ultraviolet solidified aqueous coating and preparation method thereof
A technology of water-based paint and ultraviolet light, which is applied in the direction of coating, latex paint, etc., can solve the problems of brittleness and poor flexibility
- Summary
- Abstract
- Description
- Claims
- Application Information
AI Technical Summary
Problems solved by technology
Method used
Examples
Embodiment 1
[0027] Embodiment 1: at first prepare epoxy-acrylic acid ester: add epoxy resin, hydroquinone and N, N-dimethylaniline in the there-necked flask that separatory funnel and stirring device are housed, after stirring evenly, use Acrylic acid was slowly added dropwise through the liquid funnel, and the drop was completed within 1 hour. The temperature was raised to 60° C., stirred at a rotation speed of 100 rpm, reacted for 3 hours, and cooled to room temperature. The molar ratio of epoxy resin:acrylic acid is 1:1, hydroquinone accounts for 0.01% by mass of the total mixture, and N,N-dimethylaniline accounts for 0.1% by mass of the total mixture.
[0028] Then prepare polyurethane-acrylate: add polyoxypropylene glycol, dimethylol propionic acid and stir in a three-necked flask equipped with a separatory funnel and a stirring device, then add toluene diisocyanate and dibutyltin dilaurate, and heat up to 60 React at ℃ for 3 hours, then gradually add β-hydroxyethyl acrylate dropwise...
Embodiment 2
[0033] Embodiment 2: at first prepare epoxy-acrylic acid ester: add epoxy resin, hydroquinone and N, N-dimethylaniline in the there-necked flask that separatory funnel and stirring device are housed, after stirring evenly, use dividing Acrylic acid was slowly added dropwise into the liquid funnel, and the drop was completed within 3 hours. The temperature was raised to 100° C., stirred at a rotation speed of 150 rpm, reacted for 8 hours, and cooled to room temperature. The molar ratio of epoxy resin:acrylic acid is 1.4:1, hydroquinone accounts for 1% by mass of the total mixture, and N,N-dimethylaniline accounts for 2% by mass of the total mixture.
[0034] Then prepare polyurethane-acrylate: add polytetrahydrofuran diol and dimethylol propionic acid to a three-necked flask equipped with a separatory funnel and a stirring device and stir, then add 4,4'-diphenylmethane diisocyanate and octanoic acid sulfide Tin, heat up to 100°C and react for 8 hours, then gradually add acrylat...
Embodiment 3
[0039] Embodiment 3: first prepare epoxy-acrylic acid ester: add epoxy resin, hydroquinone and N, N-dimethylaniline in the there-necked flask that separatory funnel and stirring device are housed, after stirring evenly, use Acrylic acid was slowly added dropwise into the liquid funnel, and the drop was completed within 2 hours. The temperature was raised to 80° C., stirred at 120 rpm, reacted for 6 hours, and cooled to room temperature. The molar ratio of epoxy resin:acrylic acid is 1.2:1, hydroquinone accounts for 0.5% by mass of the total mixture, and N,N-dimethylaniline accounts for 0.8% by mass of the total mixture.
[0040] Then prepare polyurethane-acrylate: add polyethylene glycol, dimethylol propionic acid and stir in a three-necked flask equipped with a separating funnel and a stirring device, then add hexamethylene diisocyanate and stannous octoate, and heat up to 70 React at ℃ for 5 hours, after cooling, gradually add acrylate-β-hydroxypropyl ester dropwise, raise the...
PUM
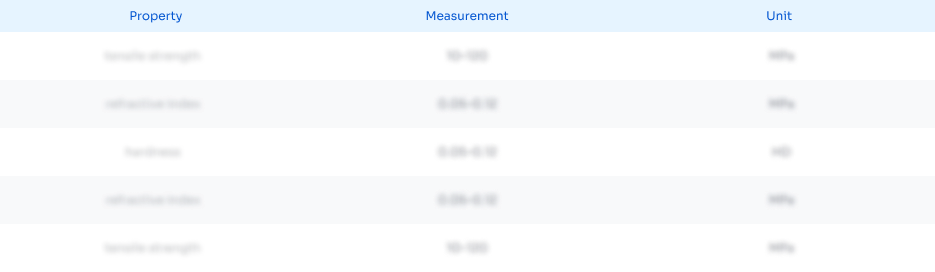
Abstract
Description
Claims
Application Information

- R&D
- Intellectual Property
- Life Sciences
- Materials
- Tech Scout
- Unparalleled Data Quality
- Higher Quality Content
- 60% Fewer Hallucinations
Browse by: Latest US Patents, China's latest patents, Technical Efficacy Thesaurus, Application Domain, Technology Topic, Popular Technical Reports.
© 2025 PatSnap. All rights reserved.Legal|Privacy policy|Modern Slavery Act Transparency Statement|Sitemap|About US| Contact US: help@patsnap.com