Selective hydrogenation desulfurization method for bastard gasoline
A technology for hydrodesulfurization and inferior gasoline, applied in refining to remove heteroatoms, etc., can solve the problems of complex process flow, high equipment capital and operating costs, simplify the operation process, improve the hydrodesulfurization selectivity, and eliminate strong inhibitory effect
- Summary
- Abstract
- Description
- Claims
- Application Information
AI Technical Summary
Problems solved by technology
Method used
Image
Examples
example 1
[0037] Preparation of a highly active WO by co-impregnation 3 (10.0wt%)-NiO(2.0wt%)-P 2 o 5 (1.5wt%) / Al 2 o 3 catalyst.
[0038] Take by weighing 1000g pseudo-thin water aluminum hydroxide powder (Al 2 o 3 Dry basis content is 78wt%), adding accounted for Al 2 o 3 Dry basis 5wt% squash powder extrusion aid, mass concentration 10% nitric acid aqueous solution 200ml, mix and roll and mix into plastic powder, use extruder to prepare cylindrical strips with a diameter of 1.5mm, dry at 120°C 8 hours, calcination at 500°C for 5 hours to prepare a catalyst carrier;
[0039] Press Catalyst on WO 3 content of 10.0wt%, NiO content of 2.0wt% and P 2 o 5 The content is 1.5wt%. Take quantitative ammonium metatungstate, nickel nitrate and phosphoric acid, add deionized water to make 100ml impregnation solution, and then spray it on 160g of the above-mentioned catalyst carrier. Drying at 120°C for 6 hours and calcining at 480°C for 6 hours prepared WO 3 (10.0wt%)-NiO(2.0wt%)-P ...
example 2
[0041] Preparation of a low activity MoO by co-impregnation 3 (3.0wt%)-CoO(1.0wt%)-K 2 O(2.0wt%) / Al 2 o 3 catalyst.
[0042] The catalyst carrier was prepared with reference to Example 1.
[0043] MoO on Catalyst 3 content of 3.0wt%, CoO content of 1.0wt% and K 2 O content is 2.0wt%, take quantitative ammonium molybdate, cobalt nitrate and potassium nitrate, add deionized water, be made into 110ml impregnation liquid, then, spray on the above-mentioned catalyst carrier of 165g. Drying at 120°C for 8 hours and calcining at 500°C for 4 hours prepared MoO 3 (3.0wt%)-CoO(1.0wt%)-K 2 O(2.0wt%) / Al 2 o 3 catalyst. The catalyst is referred to as LAC-1 for short, and the specific surface area and pore volume properties of the catalyst are shown in Table 1 by low-temperature nitrogen adsorption BET method.
example 3
[0045] Preparation of a highly active MoO by a stepwise impregnation method 3 (13.0wt%)-CoO(4.0wt%)-P 2 o 5 (1.5wt%)-K 2 O-(2.0wt%) / Al 2 o 3 catalyst.
[0046] The catalyst carrier was prepared with reference to Example 1.
[0047] Press Catalyst on P 2 o 5 The content is 1.5wt%, K 2 O content is 2.0wt%, take quantitative phosphoric acid, potassium nitrate, add deionized water, be made into 120ml impregnating solution, then, spray on the above-mentioned catalyst carrier of 160g. P 2 o 5 (1.5wt%)-K 2 O-(2.0wt%) / Al 2 o 3 Catalyst intermediate.
[0048] MoO on Catalyst 3 The content is 13.0wt%, and the CoO content is 4.0wt%. Take quantitative molybdenum oxide and basic cobalt carbonate, add deionized water to make 60ml impregnation solution, and then spray it on 80g of the above-mentioned catalyst intermediate. Highly active MoO was prepared by drying at 120°C for 8 hours and calcining at 490°C for 6 hours 3 (13.0wt%)-CoO(4.0wt%)-P 2 o 5 (1.5wt%)-K 2 O-(2.0wt%...
PUM
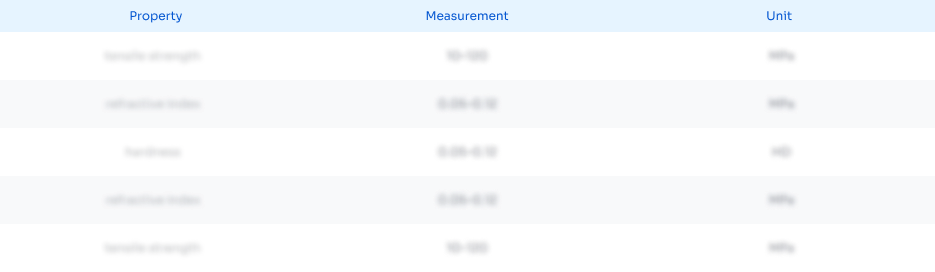
Abstract
Description
Claims
Application Information

- R&D Engineer
- R&D Manager
- IP Professional
- Industry Leading Data Capabilities
- Powerful AI technology
- Patent DNA Extraction
Browse by: Latest US Patents, China's latest patents, Technical Efficacy Thesaurus, Application Domain, Technology Topic, Popular Technical Reports.
© 2024 PatSnap. All rights reserved.Legal|Privacy policy|Modern Slavery Act Transparency Statement|Sitemap|About US| Contact US: help@patsnap.com