Destatic milling-assisting and yield-increasing technique for cement mill
A technology of cement grinding and static electricity, applied in the field of cement production, can solve the problems of clinker becoming wet, affecting cement production, affecting cement processing, etc., achieving the effect of improving grinding capacity, reducing the amount of recycled materials, and preventing static electricity
- Summary
- Abstract
- Description
- Claims
- Application Information
AI Technical Summary
Problems solved by technology
Method used
Examples
Embodiment 1
[0017] Production of clinker: According to the conventional cement production method, limestone, clay, anthracite, fluorite and pyrite powder are mixed with black raw material through the raw material computer batching system, and the raw material mill is used for grinding. Sampling and testing the percentage of calcium oxide and fineness of the raw meal once an hour, and adjust it in time; put the ground raw meal into the calcination kiln for calcination to obtain clinker, and the moisture content of the clinker is controlled at 0-2.0;
[0018] Crushing: Crushing the above-mentioned clinker in the crusher;
[0019] Drying: the mixed material is dried in the drying machine, the moisture of the mixed material is controlled at 0-2.0, and each material of the mixed material is in parts by weight, slag: gypsum: fly ash=16:6:28 .
[0020] Grinding: Put the above crushed clinker and the dried mixed material into the cement mill, inject water into the cement grinding head for grindi...
Embodiment 2
[0023] In the described grinding step, 60 tons of Portland cement clinker and admixture produced by conventional techniques are put into the cement mill, and 48Kg of water is injected into the grinding head simultaneously, and other steps are the same as in Example 1.
Embodiment 3
[0025] In the described grinding step, 60 tons of ordinary Portland cement clinker and admixture produced by conventional techniques are put into the cement mill, and 30Kg of water is injected into the grinding head at the same time, and other steps are the same as in Example 1.
PUM
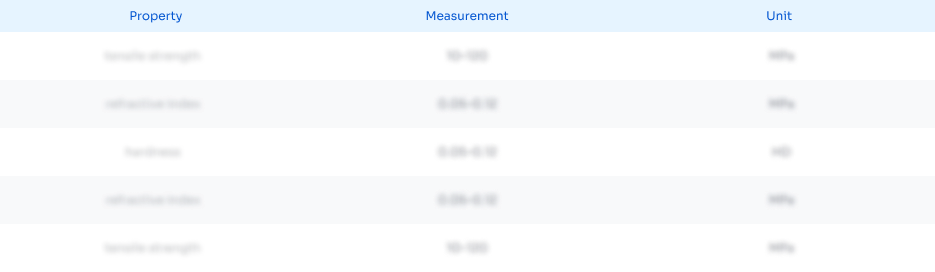
Abstract
Description
Claims
Application Information

- R&D
- Intellectual Property
- Life Sciences
- Materials
- Tech Scout
- Unparalleled Data Quality
- Higher Quality Content
- 60% Fewer Hallucinations
Browse by: Latest US Patents, China's latest patents, Technical Efficacy Thesaurus, Application Domain, Technology Topic, Popular Technical Reports.
© 2025 PatSnap. All rights reserved.Legal|Privacy policy|Modern Slavery Act Transparency Statement|Sitemap|About US| Contact US: help@patsnap.com