Method for increasing nitrogen content of nitrogen-containing clean steel
A technology for pure steel and molten steel, applied in the field of nitrogen increasing of alloy steel in metallurgical industry, can solve the problems of poor molten steel purity, poor nitrogen absorption stability, large fluctuation of nitrogen content, etc., and achieve cost reduction, low production cost, easy control effect
- Summary
- Abstract
- Description
- Claims
- Application Information
AI Technical Summary
Problems solved by technology
Method used
Image
Examples
Embodiment 1
[0031] After the nitrogen-containing steel is treated in a 100t electric furnace, refined in a 100t ladle furnace and VD vacuum degassing treatment, the nitrogen in the molten steel is 0.012% (the standard nitrogen requirement is 0.03% to 0.06%, and the target is 0.045%), and other chemical components are all qualified.
[0032] Such as figure 1 The ladle bottom blowing system is a pipeline system equipped with two sub-pipelines. On the original ladle single-circuit system, a nitrogen blowing pipeline is added to form two sub-pipelines, namely argon sub-pipeline 1 and nitrogen sub-pipeline 2. And merged into a pipeline system of the main pipeline. On-off valves and pressure gauges 3 are arranged in the sub-pipelines, and a pressure-reducing valve 5 is arranged on the main pipeline connected to the air-permeable brick 41 at the bottom of the ladle 4 .
[0033] Check the original pressure of the gas, pure argon: the pressure is 0.5Mpa, the purity is 99.99%; industrial nitrogen:...
Embodiment 2
[0040] After the nitrogen-containing steel is treated in a 100t electric furnace, refined in a 100t ladle furnace, and VD vacuum degassed, the nitrogen in the molten steel is measured to be 0.015% (standard nitrogen requirements are 0.03% to 0.06%, and the target is 0.040%), and other chemical components have been tested. qualified.
[0041] or use as figure 1 A pipeline system with two sub-pipelines, one nitrogen blowing pipeline, one argon blowing pipeline, check the original gas pressure, pure argon: pressure 0.4Mpa, purity 99.99%; industrial nitrogen: pressure 0.4Mpa, purity 99.5% %.
[0042] The first step is to close the argon, analyze the nitrogen content x0=0.015%, start blowing nitrogen, and control the pressure of nitrogen blown into the ladle to 0.45Mpa through the pressure reducing valve. Check the metallurgical handbook, and the Xe of this component steel is 0.2143% (Xe is steel The equilibrium solubility can be checked according to the two parameters of chemica...
Embodiment 3
[0048] After the nitrogen-containing steel is treated in a 60t electric furnace, refined in a 60t ladle furnace and VD vacuum degassing treatment, the measured nitrogen in the molten steel is 0.014% (the standard nitrogen requirement is 0.03% to 0.06%, and the target is 0.045%), and other chemical components have been tested. qualified.
[0049] or use as figure 1 A pipeline system with two sub-pipelines, one nitrogen blowing pipeline and one argon blowing pipeline, check the original gas pressure, pure argon: pressure 0.3Mpa, purity 99.99%; industrial nitrogen: pressure 1.0Mpa, purity 99.5% %.
[0050] The first step is to close the argon gas, analyze the nitrogen content x0=0.014%, start blowing nitrogen gas, and control the pressure of nitrogen gas blown into the ladle to 0.50Mpa through the pressure reducing valve. Check the metallurgical manual, and the Xe of this composition steel is 0.2259% (Xe is steel The equilibrium solubility can be checked according to the two pa...
PUM
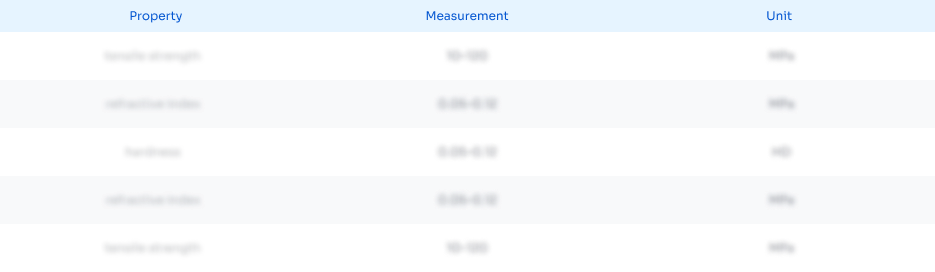
Abstract
Description
Claims
Application Information

- R&D
- Intellectual Property
- Life Sciences
- Materials
- Tech Scout
- Unparalleled Data Quality
- Higher Quality Content
- 60% Fewer Hallucinations
Browse by: Latest US Patents, China's latest patents, Technical Efficacy Thesaurus, Application Domain, Technology Topic, Popular Technical Reports.
© 2025 PatSnap. All rights reserved.Legal|Privacy policy|Modern Slavery Act Transparency Statement|Sitemap|About US| Contact US: help@patsnap.com