Functionalization polyacrylonitrile resin, production and application of the same in fibre
A technology of polyacrylonitrile resin and polyacrylonitrile fiber, which is applied in the field of functionalized polyacrylonitrile resin and its preparation and application, can solve the problems of reduced strength and lack of compatibility of modified fibers, and achieve good performance and improved modification Efficiency, the effect of excellent compatibility
- Summary
- Abstract
- Description
- Claims
- Application Information
AI Technical Summary
Problems solved by technology
Method used
Image
Examples
Embodiment 1
[0042] In the reactor with reflux condenser, electric stirrer and electric heating temperature controller, add 39g polyhexamethylenediamine hydrochloride biguanide methacrylate (molecular weight 1000) and 1300g DMSO successively, after stirring and dissolving, add 351g acrylonitrile , and gradually raised the temperature to 72°C. Then, azobisisobutyronitrile (2.0 g) dissolved in DMSO was added dropwise, and reacted for 4 hours. After the reaction, unreacted monomers were removed under reduced pressure to obtain a DMSO solution of functionalized polyacrylonitrile resin. The solid content of the solution was 19.8%, and the content of the guanidinium salt oligomer in the functionalized polyacrylonitrile was 5.6%.
[0043] After blending this solution with a conventional polyacrylonitrile / DMSO solution (solid content of 20%) at a ratio of 1:4.5 (by weight), defoaming is performed to prepare a spinning solution, which is formed by spinning, washing, stretching, Dry and densify th...
Embodiment 2
[0046] In a reactor with a reflux condenser, an electric stirrer and an electric temperature controller, add 56g of polyethylenediamine guanidine hydrochloride methacrylate (molecular weight 700) and 1300g of water successively, after stirring and dissolving, add 500g of acrylonitrile , and gradually raised the temperature to 72°C. Then, potassium persulfate (3.0 g) dissolved in water was added dropwise, and reacted for 4 hours. After the reaction, cool, filter and wash with water. The obtained copolymer white powder was vacuum-dried at 80° C. to obtain a functionalized polyacrylonitrile resin. The conversion rate of the reaction is 68.5%, and the content of the guanidinium salt oligomer in the functionalized polyacrylonitrile resin is 6.2%.
[0047] Take 160g of functionalized polyacrylonitrile resin and 800g of conventional polyacrylonitrile powder and mix them uniformly, dissolve them together in 7kg of 50% NaSCN aqueous solution to make a uniform solution with a solid co...
Embodiment 3
[0050] In the reactor with reflux condenser, electric stirrer and electric heating temperature controller, add the acrylate (molecular weight 2000) of 39g polyhexamethylenediamine guanidine nitrate and 1300g water successively, after stirring and dissolving, add 221g acrylonitrile, gradually The temperature was raised to 72°C. Then, potassium persulfate (1.3 g) dissolved in water was added dropwise, and reacted for 4 hours. After the reaction is completed, the functionalized polyacrylonitrile resin is obtained by cooling, filtering, washing with water, and vacuum drying at 80°C. It was determined that the conversion rate of the reaction was 57.6%, and the content of the guanidinium salt oligomer in the functionalized polyacrylonitrile resin was 8.8%.
[0051] Get 150g of functionalized polyacrylonitrile resin and 1200g of conventional polyacrylonitrile powder to mix evenly, dissolve in 4.1kgDMF jointly, make the homogeneous solution that solid content is 30%, defoaming, prepa...
PUM
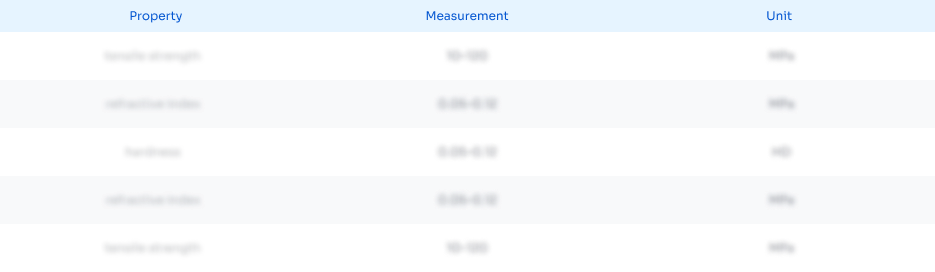
Abstract
Description
Claims
Application Information

- R&D
- Intellectual Property
- Life Sciences
- Materials
- Tech Scout
- Unparalleled Data Quality
- Higher Quality Content
- 60% Fewer Hallucinations
Browse by: Latest US Patents, China's latest patents, Technical Efficacy Thesaurus, Application Domain, Technology Topic, Popular Technical Reports.
© 2025 PatSnap. All rights reserved.Legal|Privacy policy|Modern Slavery Act Transparency Statement|Sitemap|About US| Contact US: help@patsnap.com