Method for preparing low-contraction high-fluidity high-toughness polypropylene
A high-fluidity, high-flow technology, applied in the field of low-shrinkage, high-flow and high-toughness polypropylene compositions, can solve the problems of difficult balance of fluidity, impact resistance and shrinkage rate
- Summary
- Abstract
- Description
- Claims
- Application Information
AI Technical Summary
Problems solved by technology
Method used
Examples
Embodiment 1
[0030] Table 1 Proportion of sample 1
[0031] raw material name
Dosage (weight)
High Flow Polypropylene
35phr
Polypropylene Alloy Hifax
35phr
POE
8phr
22phr
1010 / 168
0.1 / 0.2phr
770 / 944
0.2 / 0.2phr
0.2phr
[0032] Preparation:
[0033] (1) Put polypropylene resin, polypropylene alloy Hifax, 6-8 parts of superfine talc powder, toughening agent, antioxidant, weather resistance agent, and processing aid in a mixer and mix them for 3-8 minutes. obtain the mixture;
[0034] (2) Feed the remaining superfine talc powder and the mixture obtained in step (1) into twin-screw extrusion equipment through a precision metering system, melt and knead at a temperature of 195-215°C, extrude, granulate, and bake dry pack. The specific test results of the obtained products are shown in Table 2
[0035] Table 2 Test results of sample 1
[0036] ...
Embodiment 2
[0038] Table 3 Proportion of sample 2
[0039] raw material name
Dosage (weight)
High Flow Polypropylene
58phr
Polypropylene Alloy Hifax
12phr
SEBS
18phr
12phr
1010 / 168
0.1 / 0.2phr
770 / 944
0.2 / 0.2phr
0.2phr
[0040] Preparation:
[0041] (1) Put polypropylene resin, polypropylene alloy Hifax, toughening agent, antioxidant, weather resistance agent, and processing aid in a mixer and stir and mix for 3-8 minutes to obtain a mixture;
[0042] (2) Send the superfine talc powder and the mixture obtained in step (1) into the twin-screw extrusion equipment through the precision metering system, melt and knead at a temperature of 195-215°C, extrude and granulate, and dry Bag. The specific test results of the obtained products are shown in Table 2
[0043] Table 4 Test results of sample 2
[0044] performance
Embodiment 3
[0046] Table 5 Proportion of sample 3
[0047] raw material name
Dosage (weight)
High Flow Polypropylene
50phr
Polypropylene Alloy Hifax
20phr
POE
13phr
17phr
1010 / 168
0.1 / 0.2phr
770 / 944
0.2 / 0.2phr
Erucamide
0.2phr
[0048] Preparation:
[0049] (1) Put polypropylene resin, polypropylene alloy Hifax, toughening agent, antioxidant, weather resistance agent, and processing aid in a mixer and stir and mix for 3-8 minutes to obtain a mixture;
[0050] (2) Send the superfine talc powder and the mixture obtained in step (1) into the twin-screw extrusion equipment through the precision metering system, melt and knead at a temperature of 195-215°C, extrude and granulate, and dry Bag. The specific test results of the obtained products are shown in Table 2
[0051] Table 6 Test results of sample 3
[0052] performance
PUM
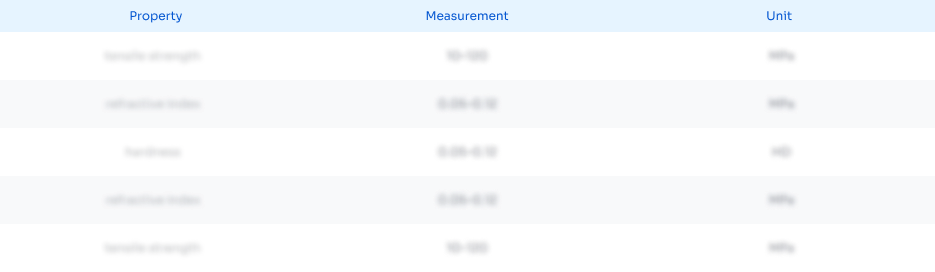
Abstract
Description
Claims
Application Information

- R&D
- Intellectual Property
- Life Sciences
- Materials
- Tech Scout
- Unparalleled Data Quality
- Higher Quality Content
- 60% Fewer Hallucinations
Browse by: Latest US Patents, China's latest patents, Technical Efficacy Thesaurus, Application Domain, Technology Topic, Popular Technical Reports.
© 2025 PatSnap. All rights reserved.Legal|Privacy policy|Modern Slavery Act Transparency Statement|Sitemap|About US| Contact US: help@patsnap.com