Fluid bed catalyst for acrylonitrile production
A technology of fluidized bed catalyst and acrylonitrile, which is applied in the direction of physical/chemical process catalyst, metal/metal oxide/metal hydroxide catalyst, bulk chemical production, etc. It can solve the problem of low acrylonitrile load and low reaction pressure, etc. problems, to achieve the effect of improving activity and stability
- Summary
- Abstract
- Description
- Claims
- Application Information
AI Technical Summary
Problems solved by technology
Method used
Image
Examples
Embodiment 1
[0052] 7.7 grams of cesium nitrate, 4.56 grams of rubidium nitrate and 2.69 grams of potassium hydroxide are added to 20 grams of water and heated to dissolve to obtain material (A); 53.6 grams of ammonium tungstate and 841.5 grams of ammonium molybdate are dissolved in 690 grams of 60~90℃ heat In water, get material (B); mix 289.0 g of bismuth nitrate, 254.6 g of magnesium nitrate, 525.1 g of nickel nitrate, 486.4 g of iron nitrate and 11.6 g of lanthanum nitrate, add 280 g of water, and heat to dissolve as material (C), weigh Dissolve 40.3 grams of chromium trioxide in 50 grams of water to obtain material (D). Weigh 17.2 grams of cerium nitrate and dissolve in 20 grams of water and heat to dissolve to obtain material (E).
[0053] Mix material (A) with 2475 grams of silica sol with a weight concentration of 40%, add materials (B), (C), (D) and (E) in sequence with stirring, and then add 140.7 grams of 50% manganese nitrate solution , After fully stirring, the slurry is obtained....
Embodiment 2~6 and comparative example 1~4
[0056] The catalysts with different active compositions in the following table were prepared by basically the same method as in Example 1, and the prepared catalyst was used to carry out the ammoxidation of propylene to acrylonitrile under the following reaction conditions. The results are shown in Table 1.
[0057] The reaction conditions of the above examples and comparative examples are:
[0058] φ38 mm fluidized bed reactor
[0059] Reaction temperature 440℃
[0060] Reaction pressure 0.14MPa
[0061] Catalyst loading amount 400g
[0062] Catalyst propylene load (WWH) 0.11 hour -1
[0063] Raw material ratio (mole) C 3 = / NH 3 / Air=1 / 1.2 / 9.8
[0064] Table 1
[0065] Example
PUM
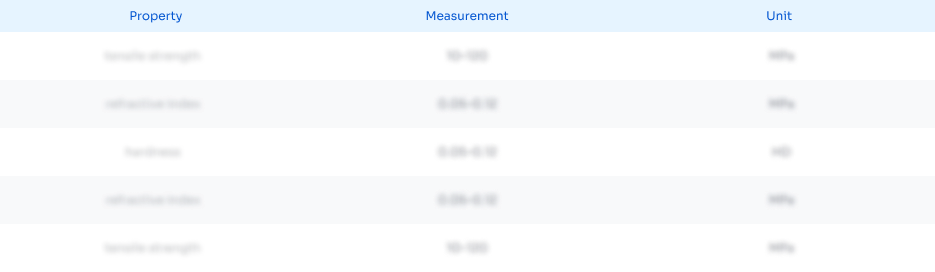
Abstract
Description
Claims
Application Information

- R&D
- Intellectual Property
- Life Sciences
- Materials
- Tech Scout
- Unparalleled Data Quality
- Higher Quality Content
- 60% Fewer Hallucinations
Browse by: Latest US Patents, China's latest patents, Technical Efficacy Thesaurus, Application Domain, Technology Topic, Popular Technical Reports.
© 2025 PatSnap. All rights reserved.Legal|Privacy policy|Modern Slavery Act Transparency Statement|Sitemap|About US| Contact US: help@patsnap.com