Continuous production method for polyoxymethylene resin
A polyoxymethylene resin and a production method technology, applied in the field of polyoxymethylene resin production technology, can solve the problems of high overall operating cost, large equipment investment, long production cycle and the like, and achieve the effects of short reaction time, low operating cost and reduced dosage
- Summary
- Abstract
- Description
- Claims
- Application Information
AI Technical Summary
Problems solved by technology
Method used
Examples
Embodiment 1
[0023] The monomer paraformaldehyde in the liquid state and the polymerization solvent dioxane are pre-mixed according to the volume ratio of 100:1; Co-rotating and counter-rotating twin-screw extruders, the working temperature of the extruder is controlled at 200°C, the rotational speed is controlled at 200r / min, and the polymerization reaction is carried out in the presence of a cationic catalyst, and the polymerization time is 0.5min. During the entire production process, there is no leakage due to the recycling of unconverted monomers and polymerization solvents. Copolyoxymethylene is obtained after the polymerization reaction is completed, and the copolyoxymethylene is packaged to obtain a finished product after proper post-treatment. Acetal copolymer products are white.
Embodiment 2
[0025] The monomer paraformaldehyde in the liquid state and the polymerization solvent propylene oxide are pre-mixed according to the volume ratio of 100:50; And counter-rotating conveying twin-screw extruder, the working temperature of the extruder is controlled at 100°C, the speed is controlled at 50r / min, and the polymerization reaction is carried out in the presence of a cationic catalyst, and the polymerization time is 10min. During the entire production process, there is no leakage due to the recycling of unconverted monomers and polymerization solvents. Homopolyoxymethylene is obtained after the polymerization reaction is completed, and the homopolyoxymethylene is packaged to obtain a finished product after proper post-processing. Homopolyoxymethylene products are white.
Embodiment 3
[0027] The monomer paraformaldehyde in the liquid state and the polymerization solvent acetone are pre-mixed according to the volume ratio of 50:100; then the mixed solution is pumped into a reverse conveying four-screw extruder with a length-to-diameter ratio of 200 at 20 ° C. Out of the extruder, the working temperature of the extruder is controlled at 100° C., the rotational speed is controlled at 30 r / min, and the polymerization reaction is carried out in the presence of a cationic catalyst, and the polymerization time is 100 minutes. During the entire production process, there is no leakage due to the recycling of unconverted monomers and polymerization solvents. Homopolyoxymethylene is obtained after the polymerization reaction is completed, and the homopolyoxymethylene is packaged to obtain a finished product after proper post-processing. Homopolyoxymethylene products are white.
PUM
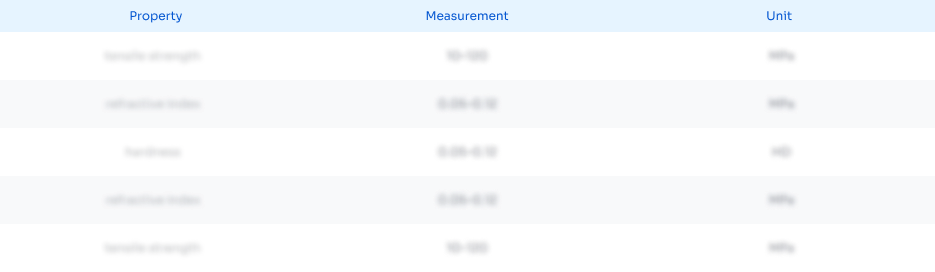
Abstract
Description
Claims
Application Information

- R&D
- Intellectual Property
- Life Sciences
- Materials
- Tech Scout
- Unparalleled Data Quality
- Higher Quality Content
- 60% Fewer Hallucinations
Browse by: Latest US Patents, China's latest patents, Technical Efficacy Thesaurus, Application Domain, Technology Topic, Popular Technical Reports.
© 2025 PatSnap. All rights reserved.Legal|Privacy policy|Modern Slavery Act Transparency Statement|Sitemap|About US| Contact US: help@patsnap.com