Method of horizontally plating, electrodepositing or electrodeless plating processing on substrate
An electrodeposition, horizontal technology, applied in the field of processing, can solve the problems of coating damage, increase the production cost of large-size substrates, poor coating uniformity, etc.
- Summary
- Abstract
- Description
- Claims
- Application Information
AI Technical Summary
Problems solved by technology
Method used
Image
Examples
Embodiment Construction
[0024] With regard to the structure and composition of the present invention, as well as the functions and advantages that can be produced, some preferred embodiments of the present invention are described in detail as follows in conjunction with the drawings.
[0025] The substrate-level metal thin film and conductive material deposition structure of the present invention are shown in Figures 3A to 3C, and please refer to the flow chart in Figure 9, the procedure is to first use the driving roller or the mechanical arm (not shown) to move the substrate 301 (the present invention) In this example, a glass substrate) is sent to the substrate support system 302 for positioning. In this embodiment, the substrate support system 302 is several rollers (step 10).
[0026] After the positioning is completed, several plating solution slow flow baffles 306 are moved and attached to the edge of the substrate 301 , and these plating solution slow flow baffles 306 surround the periphery o...
PUM
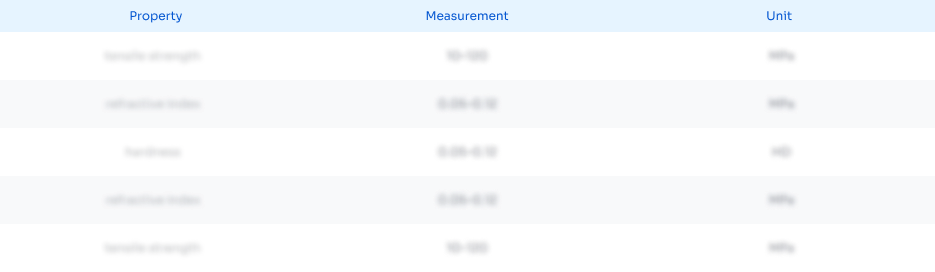
Abstract
Description
Claims
Application Information

- Generate Ideas
- Intellectual Property
- Life Sciences
- Materials
- Tech Scout
- Unparalleled Data Quality
- Higher Quality Content
- 60% Fewer Hallucinations
Browse by: Latest US Patents, China's latest patents, Technical Efficacy Thesaurus, Application Domain, Technology Topic, Popular Technical Reports.
© 2025 PatSnap. All rights reserved.Legal|Privacy policy|Modern Slavery Act Transparency Statement|Sitemap|About US| Contact US: help@patsnap.com