Method for preparing high strength cellulose and silicat composite fibre and prepared composite fibre
A silica and composite fiber technology, applied in the direction of wet spinning, etc., can solve the problems of uneven distribution of silicon in the fiber, poor physical and mechanical properties of the fiber, and limitation of the application range of the fiber, and achieve uniform distribution, low loss, and physical The effect of excellent mechanical properties
- Summary
- Abstract
- Description
- Claims
- Application Information
AI Technical Summary
Problems solved by technology
Method used
Examples
Embodiment 1
[0014] Cellulose xanthate is prepared by mixing cotton pulp and wood pulp with a polymerization degree of 811 and an α-cellulose content of 97.3% through alkali staining, pressing, crushing, and yellowing, and then using cellulose xanthate Ester, silicon dioxide (in the form of sodium silicate), sodium hydroxide and water are mixed to prepare blended viscose, and its component content (percentage by weight) is respectively: α-cellulose 8.0%, silicon dioxide 18% (for α-cellulose), sodium hydroxide 10.5%, the balance is water, mix well and dissolve, add denaturant V315 during the dissolution process, the addition amount is 2.5% (for α-cellulose), and mature , filtration, defoaming and other steps to obtain a blended spinning stock solution with a degree of esterification of 75, and the above spinning stock solution is entered into a 90g / lH 2 SO 4 , 60g / lZnSO 4 , 180g / lNa 2 SO 4 Composition, in a coagulation bath with a temperature of 35°C, silica and cellulose xanthate are c...
Embodiment 2
[0016] Using cotton pulp with a degree of polymerization of 550 and an α-cellulose content of 97.5%, cellulose xanthate was prepared through steps such as alkali staining, pressing, crushing, and yellowing, and then cellulose xanthate was prepared by using cellulose xanthate, two Silicon oxide, sodium hydroxide and water are made into colloidal solution through blending, and its component content (percentage by weight) is respectively: α-cellulose 5.0%, silicon dioxide (in the form of potassium silicate) 60% (to α -cellulose), sodium hydroxide 10.5%, the balance is water, mix well and dissolve, add denaturant V318 in the dissolution process, the addition is 1.5% (to α-cellulose), and through aging, filtration, Steps such as defoaming make the blending spinning stock solution that degree of esterification is 68, with above-mentioned spinning stock solution, enter by 90g / lH 2 SO 4 , 35g / lZnSO 4 , 190g / lNa 2 SO 4 Composition, in a coagulation bath with a temperature of 45°C, ...
Embodiment 3
[0018] Using wood pulp with a polymerization degree of 911 and an α-cellulose content of 98.5%, the cellulose xanthate is prepared through steps such as alkali staining, pressing, crushing, and yellowing, and then the cellulose xanthate is prepared by using cellulose xanthate, di Silicon oxide, sodium hydroxide and water are made into colloidal solution through blending, and its component content (percentage by weight) is respectively: α-cellulose 7.0%, silicon dioxide 40% (to α-cellulose), sodium hydroxide 10.8%, the balance is water, mix well and dissolve, add denaturant V315 during the dissolution process, the addition amount is 2.0% (for α-cellulose), and obtain esterification through aging, filtration, defoaming and other steps Degree is the blended spinning stock solution of 65, the above-mentioned spinning stock solution, enters by 60g / lH 2 SO 4 , 25g / lZnSO 4 , 130g / lNa 2 SO 4Composition, in a coagulation bath with a temperature of 35°C, silica and cellulose xanthat...
PUM
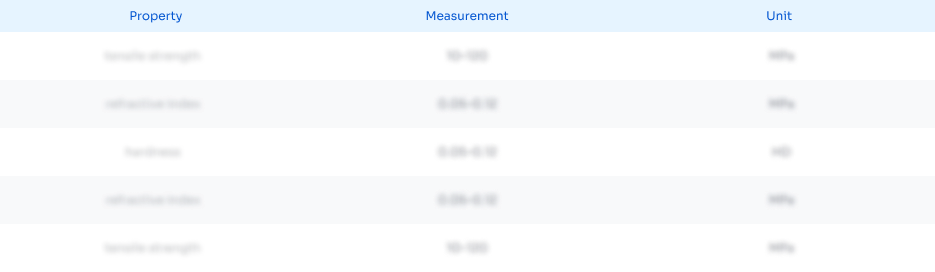
Abstract
Description
Claims
Application Information

- R&D
- Intellectual Property
- Life Sciences
- Materials
- Tech Scout
- Unparalleled Data Quality
- Higher Quality Content
- 60% Fewer Hallucinations
Browse by: Latest US Patents, China's latest patents, Technical Efficacy Thesaurus, Application Domain, Technology Topic, Popular Technical Reports.
© 2025 PatSnap. All rights reserved.Legal|Privacy policy|Modern Slavery Act Transparency Statement|Sitemap|About US| Contact US: help@patsnap.com