Self-power-supply magnetorheological intelligent vibration damping device
A technology of intelligent vibration reduction and magnetorheological damper, which is applied in vibration suppression adjustment, non-rotational vibration suppression, building components, etc., can solve the problems of large environmental interference, small induced electromotive force, and high cost, and achieve simplified semi-active damping Vibration system, system cost reduction, obvious self-adaptive features
- Summary
- Abstract
- Description
- Claims
- Application Information
AI Technical Summary
Problems solved by technology
Method used
Image
Examples
Embodiment Construction
[0024] As shown in Figure 1, the self-supplied electromagnetic rheological intelligent damping system of the present invention is mainly composed of an electromagnetically adjustable magnetorheological damper 12, a rack and pinion accelerator 13, a permanent magnet DC motor 9, and a controller 11; wherein, the The piston rod 2 of the electromagnetically adjustable magneto-rheological damper 12 is fixedly connected to the rack 6 of the rack-and-pinion accelerator 13, and the final pinion of the rack-and-pinion accelerator 13 is installed on the permanent magnet DC generator On the shaft of 9, a controller 11 is installed between the output end of the permanent magnet DC generator 9 and the electromagnetic coil terminal of the electromagnetically adjustable magnetorheological damper 12, and the rack and pinion accelerator 13 and the permanent magnet DC generator 9 is integrated into one.
[0025] Described controller 11 adopts prior art, such as using a single-chip microcomputer...
PUM
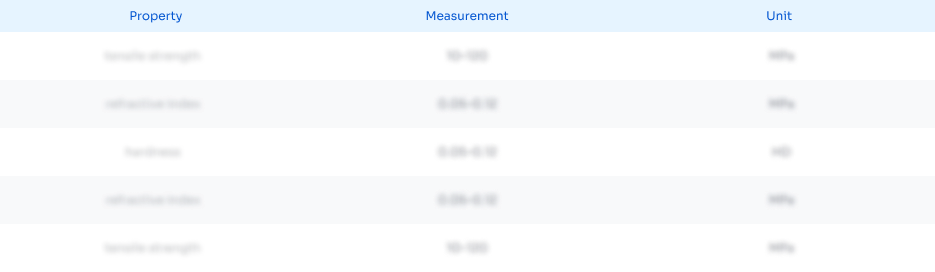
Abstract
Description
Claims
Application Information

- R&D
- Intellectual Property
- Life Sciences
- Materials
- Tech Scout
- Unparalleled Data Quality
- Higher Quality Content
- 60% Fewer Hallucinations
Browse by: Latest US Patents, China's latest patents, Technical Efficacy Thesaurus, Application Domain, Technology Topic, Popular Technical Reports.
© 2025 PatSnap. All rights reserved.Legal|Privacy policy|Modern Slavery Act Transparency Statement|Sitemap|About US| Contact US: help@patsnap.com