Copper-containing steel heating method and copper-containing steel produced by the same
A heating method and technology for copper and steel, applied in heat treatment equipment, heat treatment process control, manufacturing tools, etc., can solve problems such as low load, roll breakage, motor tripping, etc., to shorten residence time, reduce erosion, and prevent cracking.
- Summary
- Abstract
- Description
- Claims
- Application Information
AI Technical Summary
Problems solved by technology
Method used
Image
Examples
Embodiment
[0030] Table 2 shows 8 examples of heating copper-containing steel by the method of the present invention. Examples 1 to 4 are the heating methods shown in FIG. 1 ; Examples 5 to 8 are the heating methods shown in FIG. 2 . After the cast slabs heated in Examples 1 to 8 were rolled into "B" shaped steel and channel steel through a 950-800 I-800 II-850 tandem rolling mill, the surface of the shaped steel was inspected, and no cracks and cracking defects were found.
[0031] Example 1
PUM
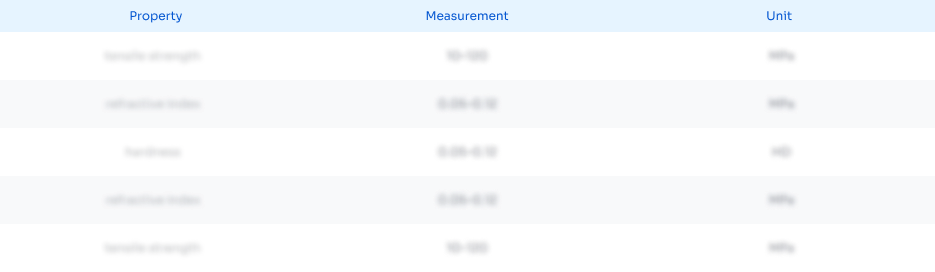
Abstract
Description
Claims
Application Information

- R&D
- Intellectual Property
- Life Sciences
- Materials
- Tech Scout
- Unparalleled Data Quality
- Higher Quality Content
- 60% Fewer Hallucinations
Browse by: Latest US Patents, China's latest patents, Technical Efficacy Thesaurus, Application Domain, Technology Topic, Popular Technical Reports.
© 2025 PatSnap. All rights reserved.Legal|Privacy policy|Modern Slavery Act Transparency Statement|Sitemap|About US| Contact US: help@patsnap.com