Vacuum grade aluminum-molybdenum-silicon alloy
A silicon alloy and vacuum technology, applied in the field of alloys, can solve the problems of serious segregation of non-vacuum grade aluminum molybdenum silicon alloy components, low molybdenum content, alloy slag inclusion, etc., and achieve the effects of uniform alloy composition, dense alloy and uniform composition.
- Summary
- Abstract
- Description
- Claims
- Application Information
AI Technical Summary
Problems solved by technology
Method used
Image
Examples
Embodiment 1
[0021] The weight composition of ingredients is based on 1kg of Al, MoO 3 0.75kg, Si 0.052kg, CaF 2 0.42kg, KClO 3 0.18kg;
[0022] Finished product composition weight percent: Mo is 40.0%, Si is 4.31%, C is 0.05%, Fe is 0.05%, H is 0.0012%, N is 0.004%, O is 0.011%, Al is balance.
Embodiment 2
[0024] The weight composition of ingredients is based on 1kg of Al, MoO 3 0.81kg, Si 0.050kg, CaF 2 0.46kg, KClO 3 .0.19kg;
[0025] Finished product composition weight percent: Mo is 42.0%, Si is 4.23%, C is 0.05%, Fe is 0.05%, H is 0.0012%, N is 0.004%, O is 0.011%, Al is balance.
[0026] Fig. 2 is the metallographic diagram enlarged by 180 times in this embodiment. It can be seen from the diagram that the alloy of the present invention has no segregation, slag inclusion and compact structure.
Embodiment 3
[0028] The weight composition of ingredients is based on 1kg of Al, MoO 3 0.99kg, Si 0.057kg, CaF 2 0.36kg;
[0029] Finished product composition weight percent: Mo is 50.8%, Si is 4.32%, C is 0.06%, Fe is 0.05%, H is 0.0014%, N is 0.005%, O is 0.013%, Al is balance.
PUM
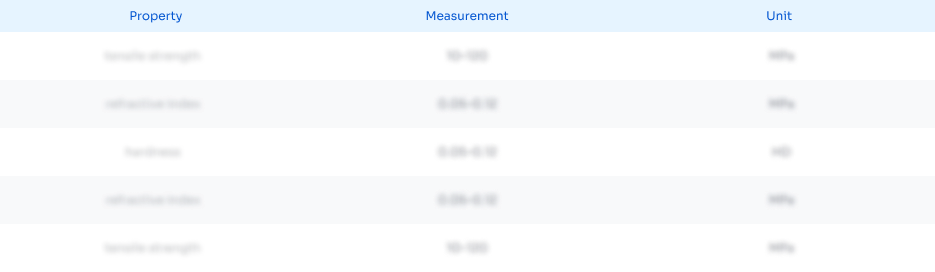
Abstract
Description
Claims
Application Information

- R&D
- Intellectual Property
- Life Sciences
- Materials
- Tech Scout
- Unparalleled Data Quality
- Higher Quality Content
- 60% Fewer Hallucinations
Browse by: Latest US Patents, China's latest patents, Technical Efficacy Thesaurus, Application Domain, Technology Topic, Popular Technical Reports.
© 2025 PatSnap. All rights reserved.Legal|Privacy policy|Modern Slavery Act Transparency Statement|Sitemap|About US| Contact US: help@patsnap.com