Activator for chemical combination of phenol by benzene hydroxide radical and the application method
An application method and catalyst technology, applied in the direction of physical/chemical process catalysts, organic compound/hydride/coordination complex catalysts, chemical instruments and methods, etc., can solve the problem of low phenol yield, loss of active components, and catalyst failure Reuse and other issues to achieve a single product, reduce pollution, and save raw materials
- Summary
- Abstract
- Description
- Claims
- Application Information
AI Technical Summary
Problems solved by technology
Method used
Examples
Embodiment 1
[0022] Preparation of Molecular Sieve-Supported Transition Metal Phthalocyanine Catalyst FePc-MCM-41
[0023] The first step: mix 1g MCM-41 molecular sieve with 10g of 5% FeSO 4 The aqueous solution was mixed, refluxed at 70°C for 24 hours, filtered, dried, and calcined at 500°C for 2 hours to obtain a powder material.
[0024] The second step: mix the powder obtained in the first step with 3.7g of phthalic anhydride, 6g of urea and 0.2g of ammonium molybdate, slowly heat up in an oil bath, and constantly stir the mixture. When the state of the mixture changes from liquid to After solidification, raise the reaction temperature to 240°C and keep it warm for 24 hours. After cooling, alternately boil and wash with dilute sodium carbonate and hydrochloric acid for 10 times, filter while hot until the filtrate is basically colorless, and then wash with ethanol until it is almost free. color, FePc-MCM-41 was obtained after drying.
Embodiment 2
[0026] Preparation of Molecular Sieve Supported Transition Metal Phthalocyanine Catalyst V / CuPc-SBA-15
[0027] Step 1: Mix 1g of SBA-15 molecular sieve with 10g of NH at the same time 4 VO 3 and 1% CuSO 4 The aqueous solution was mixed, refluxed at 90°C for 24 hours, filtered, dried, and calcined at 550°C for 4 hours to obtain a powder material.
[0028] The second step: mix the powder obtained in the first step with 7.4g of phthalic anhydride, 12g of urea and 0.5g of ammonium molybdate, slowly heat up in an oil bath, and constantly stir the mixture. When the state of the mixture changes from liquid to After solidification, raise the reaction temperature to 250°C and keep it warm for 4 hours. After cooling, alternately boil and wash with dilute sodium carbonate and hydrochloric acid for 10 times, and filter while hot until the filtrate is basically colorless. It was washed with ethanol until it was almost colorless, and V / CuPc-SBA-15 was obtained after drying.
Embodiment 3
[0030] Preparation of Molecular Sieve Supported Transition Metal Phthalocyanine Catalyst MnPc-Y
[0031] The first step: 1g Y molecular sieve and 10g content are 6% Mn(NO 3 ) 2 The aqueous solution was mixed, refluxed at 30°C for 12 hours, filtered, dried, and calcined at 500°C for 6 hours to obtain a powder material.
[0032] The second step: mix the powder obtained in the first step with 0.74g of phthalic anhydride, 2.4g of urea and 0.1g of ammonium molybdate, slowly heat up in an oil bath, and constantly stir the mixture. When the state of the mixture changes from liquid to After it is solid, raise the reaction temperature to 300°C and keep it warm for 8 hours. After cooling, it is boiled and washed 8 times with dilute sodium carbonate and hydrochloric acid alternately, and filtered while it is hot until the filtrate is basically colorless, and then washed with ethanol until Basically colorless, MnPc-Y can be obtained after drying.
PUM
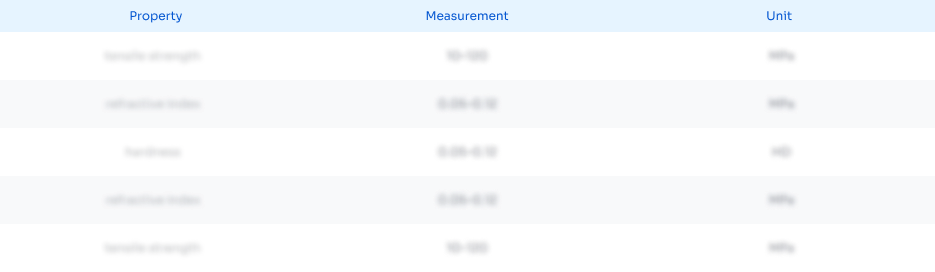
Abstract
Description
Claims
Application Information

- Generate Ideas
- Intellectual Property
- Life Sciences
- Materials
- Tech Scout
- Unparalleled Data Quality
- Higher Quality Content
- 60% Fewer Hallucinations
Browse by: Latest US Patents, China's latest patents, Technical Efficacy Thesaurus, Application Domain, Technology Topic, Popular Technical Reports.
© 2025 PatSnap. All rights reserved.Legal|Privacy policy|Modern Slavery Act Transparency Statement|Sitemap|About US| Contact US: help@patsnap.com