Method for manufacturing insole with jute fiber
The technology of jute fiber and insole is applied in the field of insole manufacturing, which can solve the problems of not being very comfortable, itching, tingling and the like, and achieve the effects of improving acupuncture performance, facilitating direct contact and improving puffing effect.
- Summary
- Abstract
- Description
- Claims
- Application Information
AI Technical Summary
Problems solved by technology
Method used
Image
Examples
Embodiment 1
[0019] The jute bought by the market is unpacked and divided into small handles of about 0.5 kg; and water bath pretreatment is carried out, the temperature of the water bath is 65 ℃, and the holding time is 2 hours; 3: 7 is mixed with compound enzyme, gets the compound enzyme prepared by weight ratio 0.5: 100 with jute, and dilutes with water to 12 times of jute weight, impregnates jute with the compound enzyme aqueous solution after dilution; Use acetic acid and small Adjust the pH value of the diluted solution with soda to 4.4, raise the temperature to 35°C, and keep it for 20 minutes; then use baking soda to adjust the pH value of the solution to 7.5, raise the temperature to 70°C, and keep it for 20 minutes; then take the jute out of the solution and pile it up In order to carry out the synergistic stacking treatment, the time for the synergistic stacking treatment is 24 hours; the jute after the synergistic stacking treatment is washed with hot water at 80°C for enzyme in...
Embodiment 2
[0022] The jute bought by the market is unpacked and divided into small handfuls of about 0.5 kilograms; and acid bath and water bath pretreatment are carried out, the acid used is the concentrated sulfuric acid with a concentration of more than 90%, and the temperature of the water bath is 30°C. The incubation time is 1 hour; the pectinase and laccase are formulated into a compound enzyme in a weight ratio of 9: 1, and the configured compound enzyme is taken in a weight ratio of 5: 100 with jute, and diluted with water to 40 times of jute weight, The jute is impregnated with the compound enzyme aqueous solution after dilution; Regulate the pH value of the diluted solution with acetic acid and baking soda to be 4.9, be warming up to 40 ℃, keep 120 minutes; 55 ℃, keep 40 minutes; Then jute is taken out from the solution and piled up to carry out synergistic stacking treatment, the time of synergistic stacking treatment is 6 hours; The jute after synergistic stacking treatment is...
Embodiment 3
[0025] The jute purchased from the market is unpacked and divided into small handfuls of about 0.5 kilograms; and the jute is carried out to an acid bath pretreatment, and the used acid is acetic acid with a concentration of more than 90%. Pectinase and laccase are formulated into compound enzyme by weight ratio 1: 1, get the compound enzyme prepared by weight ratio 1: 100 with jute, and dilute with water to 15 times of jute weight, use the compound enzyme after dilution The jute is impregnated with an aqueous solution; the pH value of the diluted solution is adjusted to 4.6 with acetic acid and baking soda, the temperature is raised to 55°C, and kept for 40 minutes; then the pH value of the solution is adjusted to 8.5 with baking soda, and the temperature is raised to 50°C, and kept for 50 minutes Then the jute is taken out from the solution and piled up for synergistic stacking, and the time for synergistic stacking is 10 hours; the jute after the synergistic stacking is clea...
PUM
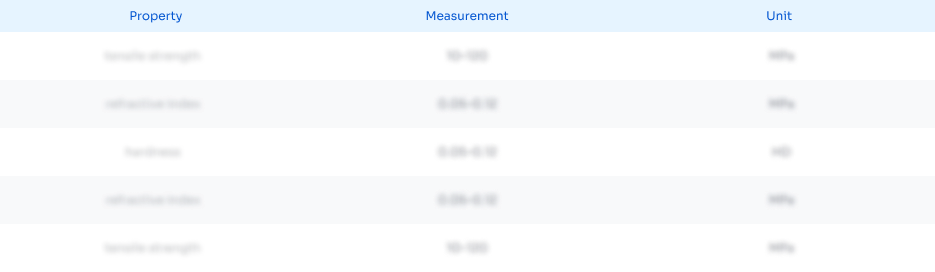
Abstract
Description
Claims
Application Information

- R&D
- Intellectual Property
- Life Sciences
- Materials
- Tech Scout
- Unparalleled Data Quality
- Higher Quality Content
- 60% Fewer Hallucinations
Browse by: Latest US Patents, China's latest patents, Technical Efficacy Thesaurus, Application Domain, Technology Topic, Popular Technical Reports.
© 2025 PatSnap. All rights reserved.Legal|Privacy policy|Modern Slavery Act Transparency Statement|Sitemap|About US| Contact US: help@patsnap.com