Rotor position presuming method and apparatus, motor control method and compressor
A technology of rotor position and control method, which is used in electronic commutation motor control, motor generator control, AC motor control and other directions to achieve the effects of improving position estimation accuracy, easy design, and good stability characteristics
- Summary
- Abstract
- Description
- Claims
- Application Information
AI Technical Summary
Problems solved by technology
Method used
Image
Examples
Embodiment Construction
[0085] Hereinafter, an embodiment of the rotor position estimation method of the present application will be described in detail with reference to the drawings.
[0086] This implementation forms a 180° sine wave sensorless control technology involving permanent magnet motors (DC brushless motors, IPM motors) with salient poles. Such as Image 6 As shown, in the 180° sine wave sensorless control, the d-q axis actual rotating coordinate system composed of the position in the direction of the permanent magnet rotor flux, that is, the d-axis and the q-axis that is 90° ahead of the d-axis in the direction of rotation, and the control The axis offset Δθ between the virtual rotor position γ-axis on the γ-axis and the γ-δ axis formed from the γ-axis ahead of the δ-axis in the direction of rotation by 90° is controlled to be zero.
[0087] Since the angle θ of the rotor (rotor position) is an integral value of the angular velocity ω of the rotor, when the position offset (Δθ) is cont...
PUM
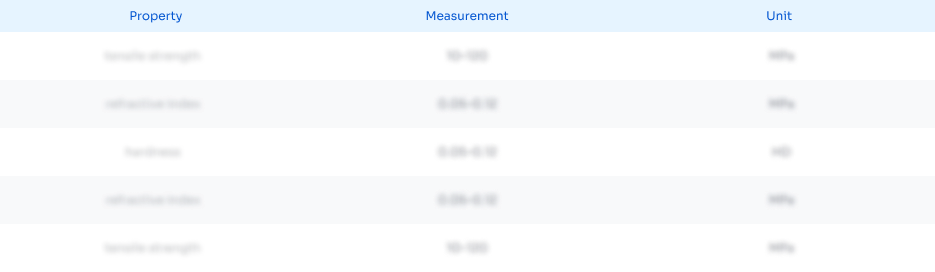
Abstract
Description
Claims
Application Information

- R&D
- Intellectual Property
- Life Sciences
- Materials
- Tech Scout
- Unparalleled Data Quality
- Higher Quality Content
- 60% Fewer Hallucinations
Browse by: Latest US Patents, China's latest patents, Technical Efficacy Thesaurus, Application Domain, Technology Topic, Popular Technical Reports.
© 2025 PatSnap. All rights reserved.Legal|Privacy policy|Modern Slavery Act Transparency Statement|Sitemap|About US| Contact US: help@patsnap.com