Launder for casting molten copper
A launder, molten metal technology, used in the field of manufacturing and casting molten metal, can solve problems such as cooling hot metal, achieve the effect of reducing blockage, avoiding local thermal stress, and avoiding cracking
- Summary
- Abstract
- Description
- Claims
- Application Information
AI Technical Summary
Problems solved by technology
Method used
Image
Examples
Embodiment Construction
[0030] figure 1 A launder structure 10 is shown, comprising a cover part 5 and a lower launder, both comprising a metal casing, such as a steel sleeve 1,2. The heating resistor circuit 3 is arranged on a support cross-arm 32 in a groove defined by the ceramic wool insulation 11 of the cover 5 . The support cross arms 32 are arranged at equal intervals below the resistor circuit 3 . A ceramic thermal insulator 33 is arranged in the heatable region of the transverse arm 32 . The current feed terminals 31 of the heating resistor 3 pass through the cover and the insulating lining 11 of the metal jacket 1 . The molten metal 4 flows into the flow channel formed by the refractory lining 22 . The refractory lining 22 is formed from an embedded composition. The ceramic wool insulation layer 21 is arranged between the refractory lining 22 and the steel sleeve 2 . The cover 5 is placed on the lower runner, supported by it, substantially preventing gas flow and heat radiation on the ...
PUM
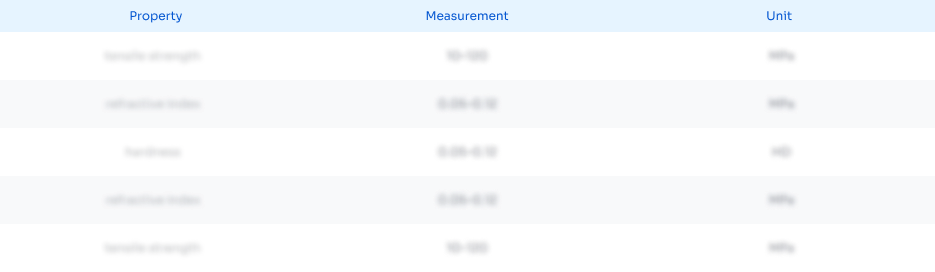
Abstract
Description
Claims
Application Information

- Generate Ideas
- Intellectual Property
- Life Sciences
- Materials
- Tech Scout
- Unparalleled Data Quality
- Higher Quality Content
- 60% Fewer Hallucinations
Browse by: Latest US Patents, China's latest patents, Technical Efficacy Thesaurus, Application Domain, Technology Topic, Popular Technical Reports.
© 2025 PatSnap. All rights reserved.Legal|Privacy policy|Modern Slavery Act Transparency Statement|Sitemap|About US| Contact US: help@patsnap.com