End position style grinding roller grinder
A technology of grinding rollers and mills, applied in grain processing, etc., can solve the problems of affecting the grinding effect, unstable operation, and upward jumping of the grinding cylinder, and achieve the effect of fineness, stable operation, and increased rotation speed of the grinding cylinder
- Summary
- Abstract
- Description
- Claims
- Application Information
AI Technical Summary
Problems solved by technology
Method used
Image
Examples
Embodiment 1
[0019] Example 1, see figure 1 , figure 2 .
[0020] It includes a grinding cylinder 1, and the lower part of the grinding cylinder 1 is provided with a grinding cylinder supporting seat 2. The grinding cylinder supporting seat 2 can be a sliding bearing structure, or a supporting wheel structure with multi-point support in the circumferential direction, or a rolling bearing structure, and At least one group is arranged along the axial direction of the grinding cylinder 1, and the figure shows the schematic structure of the sliding bearing; one end of the grinding cylinder 1 has an end cover 8, and the grinding cylinder 1 is equipped with a grinding roller 3, a roller shaft 4, a scraper and a material guide The device 5, the scraper and the material guide device can be combined into one. The illustrated part 5 is a schematic diagram of the combination of the scraper and the material guide device. The scraper and the material guide device 5 can also be independently produced....
Embodiment 2
[0024] Example 2, see Figure 4 .
[0025] Figure 4 It is a modified implementation structure of the present invention, which provides another structural form of the discharge port 10 .
[0026] Figure 4 Among them, the outer section of the ring member 12 is a cylindrical section structure 16, and is provided with a screw discharge device 17 placed in the ring member 12, the inner end of the screw discharge device has a material inlet 18, and the screw discharge device The outer section of the device is located in the cylindrical section structure 16 of the outer section of the ring member 12, and is joined and connected with the inner wall of the cylindrical section structure 16. The discharge port 10 is located between the screw discharge device 17 and the cylindrical section structure 16. On the cylinder wall of the joint part, and several are arranged along the circumference of the cylinder wall. There is also a deflector 19 in the grinding cylinder 1 that allows the ...
Embodiment 3
[0028] Example 3, see Figure 5 , Image 6 .
[0029] This example structure is based on embodiment 1 or embodiment 2, Figure 5 Represented is based on the structure of embodiment 1, on the inner section of the roller shaft 4, a grinding roller frame 21 is set, and the grinding roller frame 21 is provided with two described grinding rollers 3, and the grinding roller frame 21 can also be Three or more grinding rollers 3 are arranged, that is, at least two of the grinding rollers 3 are arranged on the grinding roller frame 21, and the scraper and the material guide device 5 are arranged between the adjacent two grinding rollers. A grinding roller 3 can form a plurality of running-in surfaces with the inner wall of the grinding cylinder 1, which is beneficial to improve production efficiency; the transmission shaft 13 is provided with a circumferential support 14, and a second circumferential support 14 as described in Example 2 can also be provided at the same time. Support...
PUM
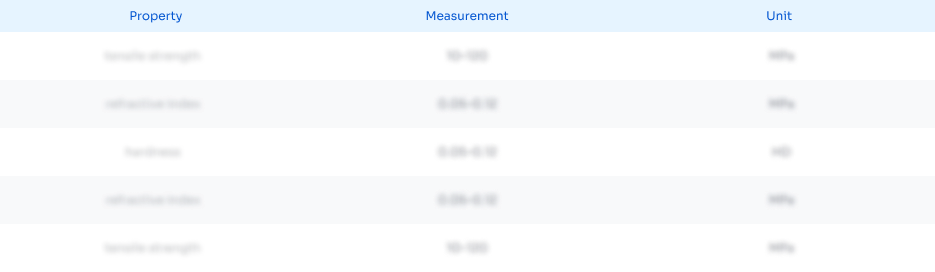
Abstract
Description
Claims
Application Information

- Generate Ideas
- Intellectual Property
- Life Sciences
- Materials
- Tech Scout
- Unparalleled Data Quality
- Higher Quality Content
- 60% Fewer Hallucinations
Browse by: Latest US Patents, China's latest patents, Technical Efficacy Thesaurus, Application Domain, Technology Topic, Popular Technical Reports.
© 2025 PatSnap. All rights reserved.Legal|Privacy policy|Modern Slavery Act Transparency Statement|Sitemap|About US| Contact US: help@patsnap.com