Method for making base-board of liquid crystal display
A technology of liquid crystal display and manufacturing method, which is applied in semiconductor/solid-state device manufacturing, instrumentation, optics, etc., can solve the problems of simplifying the manufacturing process and not being able to meet the etching bevel angle at the same time, and achieve simplified manufacturing process, improved adhesion and electrical properties, The effect of reducing the production cost
- Summary
- Abstract
- Description
- Claims
- Application Information
AI Technical Summary
Problems solved by technology
Method used
Image
Examples
Embodiment 1
[0046] see image 3 Among (a) to (h), it is a flow chart of manufacturing the substrate for liquid crystal display in a preferred embodiment of the present invention, and the substrate for thin film transistor liquid crystal display manufactured in this embodiment adopts a four-pass photomask process.
[0047] Such as image 3 As shown in (a), first a transparent glass substrate 3 is provided, a first metal layer 31 is formed on the surface of the substrate 3, and a first yellow light and etching process is performed to complete the pattern of the gate layer. Wherein, the first metal layer 31 in this example is composed of chromium alloy and molybdenum metal, and its structure can be a single-layer or multi-layer structure (not shown in the figure).
[0048] Next, if image 3 As shown in (b), an insulating layer 32, a semiconductor layer 33, an ohmic contact layer 34, and a barrier layer 35 are deposited to cover the first metal layer 31; wherein the insulating layer 32 is a...
Embodiment 2
[0061] The manufacturing method of the substrate for the thin film transistor liquid crystal display of this embodiment is the same as the four-pass photomask process described in the first embodiment, except that the semiconductor layer is a multi-layer structure and the insulating layer etching conditions are adjusted, it is roughly similar to the embodiment. Content shown in Example 1.
[0062] The semiconductor layer of this embodiment is mainly composed of a multi-layer structure, wherein the semiconductor layer includes a low deposition rate silicon layer and a high deposition rate silicon layer to form a first metal layer / first insulating layer / low deposition rate on the surface of the substrate Multi-layer film structure of silicon layer / high deposition rate silicon layer / ohmic contact layer / barrier layer.
[0063] In this example, the high deposition rate of the silicon layer helps to reduce the deposition time of the semiconductor layer and increase the production ef...
Embodiment 3
[0072] The manufacturing method of the substrate for the thin film transistor liquid crystal display of this embodiment is the same as the process conditions described in the second embodiment, which is also a four-pass photomask process. Except that the semiconductor layer adopts the single-layer structure of the first embodiment, the remaining process conditions, such as : The etching gas and the interlayer structure of other film layers of the thin film transistor are roughly similar to those shown in the second embodiment.
PUM
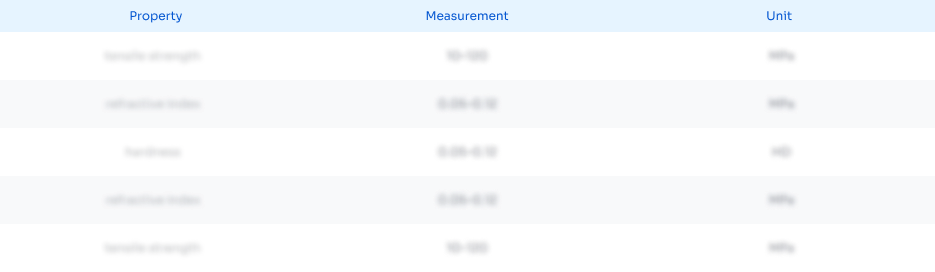
Abstract
Description
Claims
Application Information

- Generate Ideas
- Intellectual Property
- Life Sciences
- Materials
- Tech Scout
- Unparalleled Data Quality
- Higher Quality Content
- 60% Fewer Hallucinations
Browse by: Latest US Patents, China's latest patents, Technical Efficacy Thesaurus, Application Domain, Technology Topic, Popular Technical Reports.
© 2025 PatSnap. All rights reserved.Legal|Privacy policy|Modern Slavery Act Transparency Statement|Sitemap|About US| Contact US: help@patsnap.com