Aviation aluminum alloy pre-stretching plate and production method thereof
A production method and pre-stretching technology are applied in the field of aluminum alloy pre-stretched sheet and its production, which can solve the problems of deformation processing yield of aluminum alloy sheet and other problems.
- Summary
- Abstract
- Description
- Claims
- Application Information
AI Technical Summary
Problems solved by technology
Method used
Examples
specific Embodiment approach 1
[0004] Embodiment 1: In this embodiment, the pre-stretched aluminum alloy sheet for aviation is composed of 0.20 parts of Si, 0.30 parts of Fe, 1.7 parts of Cu, 0.10 parts of Mn, 0.22 parts of Cr, 0.06 parts of Cr, and 0.06 parts by weight. 100 parts of Ti, 2.5 parts of Mg, 5.60 parts of Zn, and the balance of Al.
specific Embodiment approach 2
[0005] Specific embodiment 2: The production method of the aluminum alloy pre-stretched sheet for aviation in this embodiment is realized by the following steps: 1. According to the ratio of parts by weight, 0.20 parts of Si, 0.30 parts of Fe, 1.7 parts of Cu, 0.10 parts of Mn, 0.22 parts of Cr, 0.06 parts of Ti, 2.5 parts of Mg, 5.60 parts of Zn, and the balance of Al were mixed, for a total of 100 parts. 2. Smelting the mixed metal at 700-750°C for 5-12 hours, then casting the smelted metal at a temperature of 690-705°C and a casting speed of 55-60mm / min, and Cast the metal into an ingot with a cross-sectional size of 300×1200mm; 3. Soak the ingot at a temperature of 450-460°C for 40-42 hours, and then plan the soaked ingot by conventional methods according to actual needs Edge, sawing and milling; 4. Under the temperature of 370~410℃, hot-roll the ingot according to actual needs to control the thickness of the wool, and cut the length of the wool; Quenching is carried out ...
specific Embodiment approach 3
[0006] Embodiment 3: The difference between this embodiment and Embodiment 2 is that in step 2, the mixed metals are smelted at 710-740° C. for 6-10 hours. Other steps are the same as in the second embodiment.
PUM
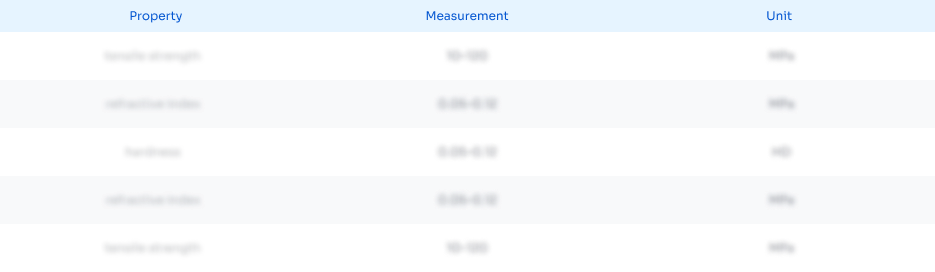
Abstract
Description
Claims
Application Information

- R&D
- Intellectual Property
- Life Sciences
- Materials
- Tech Scout
- Unparalleled Data Quality
- Higher Quality Content
- 60% Fewer Hallucinations
Browse by: Latest US Patents, China's latest patents, Technical Efficacy Thesaurus, Application Domain, Technology Topic, Popular Technical Reports.
© 2025 PatSnap. All rights reserved.Legal|Privacy policy|Modern Slavery Act Transparency Statement|Sitemap|About US| Contact US: help@patsnap.com