Method for manufacturing high-efficiency silicon solar cell via phosphorus boron synchronous diffusion
A technology for silicon solar cells and phosphorus diffusion, which is applied in final product manufacturing, sustainable manufacturing/processing, semiconductor/solid-state device manufacturing, etc. The effect of low production cost and maintaining efficiency
- Summary
- Abstract
- Description
- Claims
- Application Information
AI Technical Summary
Problems solved by technology
Method used
Image
Examples
Embodiment Construction
[0011] A method for simultaneously diffusing phosphorus and boron to manufacture high-efficiency silicon solar cells, comprising boron and phosphorus diffusion steps, boron and phosphorus diffusion adopts the following steps: take a source sheet 2 with a plurality of parallel grooves 1, place a The left and right halves of the groove are coated with SiO by APCVD method (that is, atmospheric pressure chemical vapor deposition method) or coating method. 2 / B 2 o 3 , SiO 2 / P 2 o 5 The glass body is dried at 200-600°C (for example, 200°C, 300°C, 400°C, 500°C, 600°C), and then a silicon chip 3 with the same dimensions as the source chip is inserted in the center of each groove to make the silicon chip 3 Perpendicular to the source sheet 2, perform diffusion treatment at 950-1100°C (eg 950°C, 1000°C, 1050°C, 1100°C) for 10-60 minutes (eg 10 minutes, 30 minutes, 60 minutes), during the diffusion treatment, Protected with nitrogen, the flow rate of nitrogen is 20-30 liters / minut...
PUM
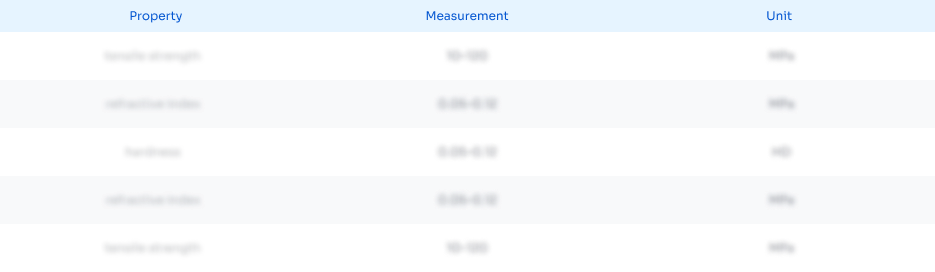
Abstract
Description
Claims
Application Information

- R&D Engineer
- R&D Manager
- IP Professional
- Industry Leading Data Capabilities
- Powerful AI technology
- Patent DNA Extraction
Browse by: Latest US Patents, China's latest patents, Technical Efficacy Thesaurus, Application Domain, Technology Topic, Popular Technical Reports.
© 2024 PatSnap. All rights reserved.Legal|Privacy policy|Modern Slavery Act Transparency Statement|Sitemap|About US| Contact US: help@patsnap.com