Ultrasound/mechanical composite grinding/polishing method and apparatus for optical fiber connector interface
An optical fiber connector and polishing device technology, which is applied to machine tools suitable for grinding workpiece edges, coupling of optical waveguides, grinding/polishing equipment, etc. Fiber end face damage and other problems, to shorten the grinding and polishing time, reduce the pressure, and improve the quality
- Summary
- Abstract
- Description
- Claims
- Application Information
AI Technical Summary
Problems solved by technology
Method used
Image
Examples
Embodiment Construction
[0036] Fig. 1 shows the overall structure of the ultrasonic / mechanical composite grinding and polishing device of the optical fiber connector end face of the present invention: the rotation motor 11 and the revolution motor 12 controlled by the control system are installed in the frame 13 to drive the grinding and polishing disc 14; The installed positioning guide rod 10 is equipped with a height adjustment device 5 and a lifting sleeve 4 connected with the outer cover 6 through a hinge 16; one end of the horn 3 passes through the horn clamp 9 and is connected with the ultrasonic transducer 7, and the other end is connected with the ultrasonic transducer 7. The ferrule body jig 2 installed with the optical fiber connector 1 is connected; the loading device 17 is arranged on the luffing jig 9 . In order to adjust the contact pressure between the end face of the optical fiber ferrule body 1 and the grinding and polishing disc 14 .
[0037] The rotation motor 11 and the revolutio...
PUM
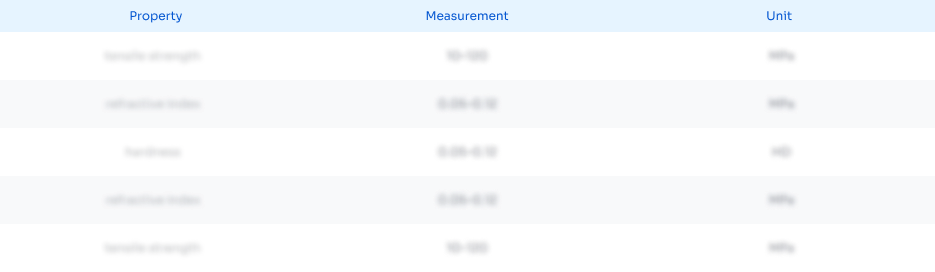
Abstract
Description
Claims
Application Information

- R&D
- Intellectual Property
- Life Sciences
- Materials
- Tech Scout
- Unparalleled Data Quality
- Higher Quality Content
- 60% Fewer Hallucinations
Browse by: Latest US Patents, China's latest patents, Technical Efficacy Thesaurus, Application Domain, Technology Topic, Popular Technical Reports.
© 2025 PatSnap. All rights reserved.Legal|Privacy policy|Modern Slavery Act Transparency Statement|Sitemap|About US| Contact US: help@patsnap.com