Grinding structural unit
A component and grinding disc technology, which is applied in the direction of abrasive materials, metal processing equipment, manufacturing tools, etc., can solve the problems of reduced grinding rate, reduced grinding rate of ground objects, and limitation of process width, so as to reduce the problem of load effect and increase the grinding rate , Improve the effect of process width
- Summary
- Abstract
- Description
- Claims
- Application Information
AI Technical Summary
Problems solved by technology
Method used
Image
Examples
no. 1 example
[0046] FIG. 2 is a schematic cross-sectional view of a grinding member according to a preferred embodiment of the present invention. Referring to FIG. 2 , the polishing member 200 of the present invention is composed of a polishing pad 210 , a polishing pad 220 and a polishing disc (platen) 230 .
[0047] Please continue to refer to Fig. 2, the grinding pad 210 is configured on the grinding pad 220, in the present embodiment, the main body of the grinding pad 210 is, for example, an emery cloth type (fixed abrasive) grinding pad, and the grinding pad 210 includes a plurality of abrasive grains (here In Fig. 2, for the sake of simplification, what is drawn is the whole layer of polishing pad 210 and does not draw individual abrasive grains), wherein these abrasive grains are arranged in a triangular pyramid, hexagonal pyramid or cylindrical shape and matrix, and each An abrasive grain is composed of a binder and abrasive grains (abrasive) uniformly distributed in the binder, an...
no. 2 example
[0056] FIG. 6 is a schematic cross-sectional view of a grinding member according to another preferred embodiment of the present invention. In addition, in FIG. 6 , the same components as in FIG. 2 are denoted by the same reference numerals, and description thereof will be omitted. Referring to FIG. 6 , the grinding member 200 of the present invention is composed of a grinding pad 210 , a grinding pad 220 and a grinding disc 230 . The difference between this embodiment and the first embodiment is that the grooves 229 and the convex structures 228 are arranged on the surface 226 of the grinding pad 220 that is in contact with the grinding disc 230. At this time, the grinding pad 220 is preferably deformable. The material is, for example, rubber, and the pattern of the formed groove 229 is, for example, the patterns shown in FIGS. 3A to 3D or one of the combinations of these patterns.
[0057] When the grinding member 200 of this embodiment is used for grinding, the grinding pad...
no. 3 example
[0059] FIG. 7 is a schematic cross-sectional view of a grinding member according to another preferred embodiment of the present invention. In addition, in FIG. 7 , the same components as those in FIG. 2 are denoted by the same reference numerals, and description thereof will be omitted. Referring to FIG. 7 , the grinding member 200 of the present invention is composed of a grinding pad 210 , a grinding pad 220 and a grinding disc 230 . This embodiment differs from the first embodiment in that the surface 222 of the grinding pad 220 in contact with the grinding pad 210 is provided with grooves 225 and convex structures 224, and the surface 226 in contact with the grinding disc 230 is also provided with There are grooves 229 and protruding structures 228 , and the pattern of the formed grooves 229 is, for example, the patterns shown in FIGS. 3A to 3D or one of the combinations of these patterns.
[0060] When using the grinding member 200 of this embodiment for grinding, the gr...
PUM
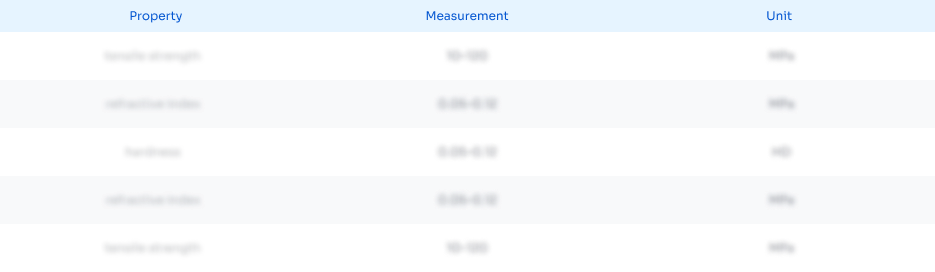
Abstract
Description
Claims
Application Information

- R&D
- Intellectual Property
- Life Sciences
- Materials
- Tech Scout
- Unparalleled Data Quality
- Higher Quality Content
- 60% Fewer Hallucinations
Browse by: Latest US Patents, China's latest patents, Technical Efficacy Thesaurus, Application Domain, Technology Topic, Popular Technical Reports.
© 2025 PatSnap. All rights reserved.Legal|Privacy policy|Modern Slavery Act Transparency Statement|Sitemap|About US| Contact US: help@patsnap.com